I'm working with a supplier to produce a compression molded phenolic resin based friction rotor.
They had some problems with the first trial; the part has splits (mostly at tool mating line) and the flash had a strange sponge/honeycomb structure.
We have no experience in molding so are looking at having to run systematic trials to find some parameters that work, to help narrow our search can anyone identify potential causes for this sort of defect?
Material:
- Novolac Phenolic Resin based (50 - 60%) + Fibre Filler (15 - 25%).
Trial Process:
- Pre-heat; 40s in 900w microwave. (minimum time found to get material to flow).
- Compression mold; 150, 160, 170, 180oC, cure time 180s, pressure ?, rate ?.
They had some problems with the first trial; the part has splits (mostly at tool mating line) and the flash had a strange sponge/honeycomb structure.
We have no experience in molding so are looking at having to run systematic trials to find some parameters that work, to help narrow our search can anyone identify potential causes for this sort of defect?
Material:
- Novolac Phenolic Resin based (50 - 60%) + Fibre Filler (15 - 25%).
Trial Process:
- Pre-heat; 40s in 900w microwave. (minimum time found to get material to flow).
- Compression mold; 150, 160, 170, 180oC, cure time 180s, pressure ?, rate ?.
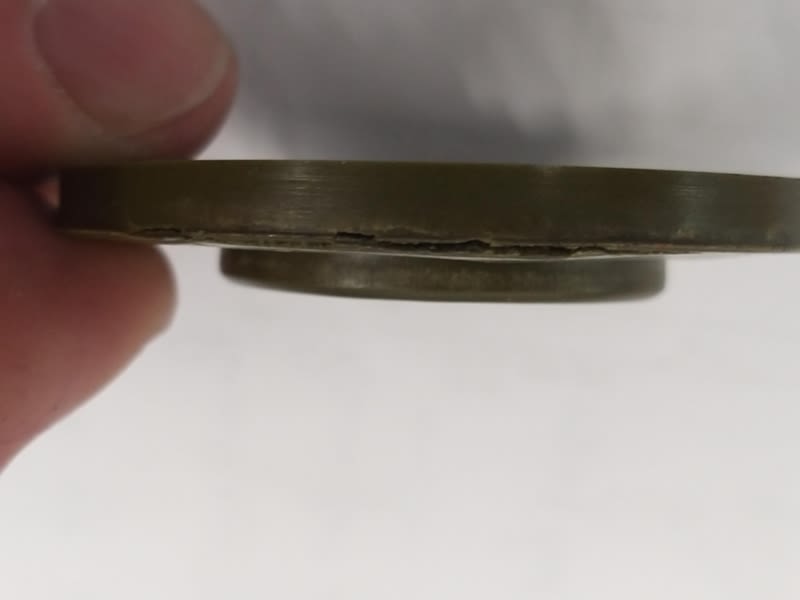
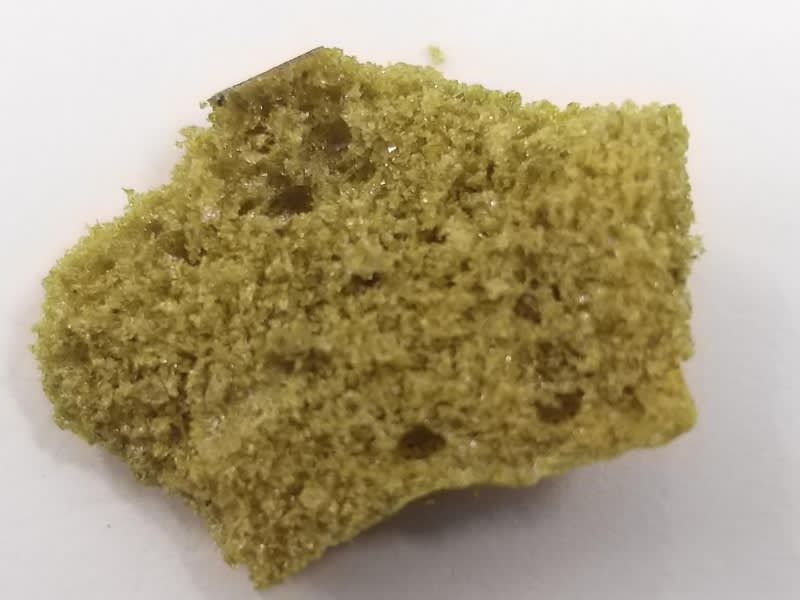