silver2164
Structural
In designing a pile cap using strut and tie method, AS3600 notes the compression strut area, Ac, as the ‘smallest cross-sectional area of the concrete strut at any point along its length and measured normal to the line of action of the strut’ (cl.7.2.3). It is also shown in Figure 7.2.4(A) that the strut has uniform depth, dc. It does not provide any further guidance on how to calculate strut area, strut depth, and strut width (Ac, dc, bc respectively).
Figure 7.2.4(A) would infer that the strut dimensions are determined by the column size and strut angle, θ (this is assuming the column is smaller than the pile). This would make sense to me. In the figure attached, this is denoted as ‘dc1’.
At the bottom of the strut, the CCT node depth could be enlarged with an extended node per ACI method. This is denoted as ‘dc2’ in the attached. My interpretation is this depth could be used to calculate the stresses at the CCT node but not for the capacity of the strut.
I have seen some designers base the strut depth on the pile size only, not the column. This is denoted as ‘dc3’ in the attached. I do not think this is appropriate as there is insufficient area to get the load transfer into the column at the top.
Fourth approach is to keep increasing strut width (dc4) until strut capacity = demand, while still checking the CCC node for the smaller node widths.
Wanting to get some other designers’ opinion on how to calculate the strut dimensions. If I just ignore the column, the strut capacity is massive and easily sufficient. By basing it off the column size, the strut size and capacity becomes limiting and the column size ends up governing the pile cap design.
In addition, finding the strut area is simple for a 2-pile cap. For 3-pile and 4-pile caps, does the strut shape remain rectangular with dimensions dc x bc? I have seen an example, based on Eurocode, where the CCC node at the top becomes a pyramid shape and the struts are triangular. This would severely reduce the strut capacity.
Second query on bursting reinforcement. AS3600 Cl.7.2.4 requires bursting reinforcement to be provided when bursting force exceeds bursting capacity. This happens in most cases as the bursting capacity is quite low. However, I very rarely seen pile caps with bursting reinforcement. I have seen previous threads on this topic in this forum, with no clear resolution.
ACI318-19 allows for design of pile caps without bursting reinforcement. The strut capacity decreases but still gives reasonable capacity.
I’ve had designers say they provide side bars, and top and bottom bars, fully lapped ‘preventing the cap from bursting out’, and just ignore this clause, while keeping the full strut capacity.
My view is not providing bursting reinforcement is not compliant with AS3600. But other codes, or ‘rational method of analysis’ could be used to justify?
How do other designers deal with the AS3600 requirement for bursting reinforcement?
Figure 7.2.4(A) would infer that the strut dimensions are determined by the column size and strut angle, θ (this is assuming the column is smaller than the pile). This would make sense to me. In the figure attached, this is denoted as ‘dc1’.
At the bottom of the strut, the CCT node depth could be enlarged with an extended node per ACI method. This is denoted as ‘dc2’ in the attached. My interpretation is this depth could be used to calculate the stresses at the CCT node but not for the capacity of the strut.
I have seen some designers base the strut depth on the pile size only, not the column. This is denoted as ‘dc3’ in the attached. I do not think this is appropriate as there is insufficient area to get the load transfer into the column at the top.
Fourth approach is to keep increasing strut width (dc4) until strut capacity = demand, while still checking the CCC node for the smaller node widths.
Wanting to get some other designers’ opinion on how to calculate the strut dimensions. If I just ignore the column, the strut capacity is massive and easily sufficient. By basing it off the column size, the strut size and capacity becomes limiting and the column size ends up governing the pile cap design.
In addition, finding the strut area is simple for a 2-pile cap. For 3-pile and 4-pile caps, does the strut shape remain rectangular with dimensions dc x bc? I have seen an example, based on Eurocode, where the CCC node at the top becomes a pyramid shape and the struts are triangular. This would severely reduce the strut capacity.
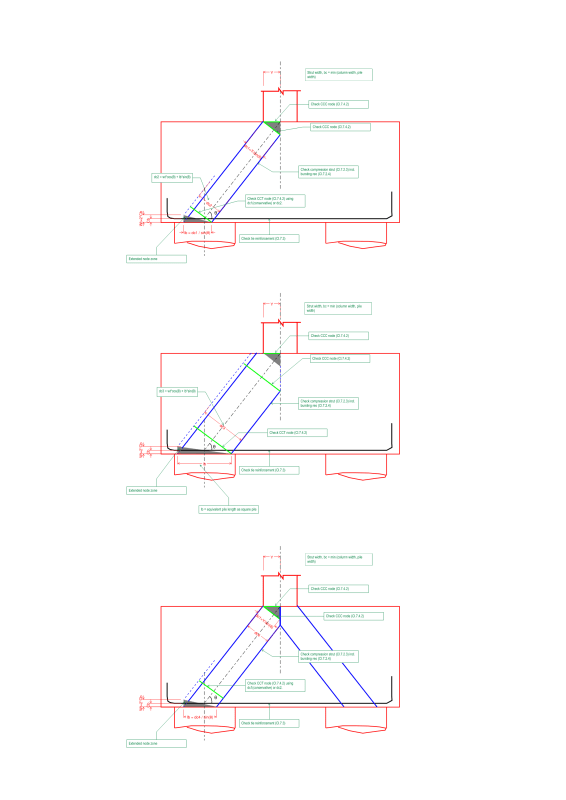
Second query on bursting reinforcement. AS3600 Cl.7.2.4 requires bursting reinforcement to be provided when bursting force exceeds bursting capacity. This happens in most cases as the bursting capacity is quite low. However, I very rarely seen pile caps with bursting reinforcement. I have seen previous threads on this topic in this forum, with no clear resolution.
ACI318-19 allows for design of pile caps without bursting reinforcement. The strut capacity decreases but still gives reasonable capacity.
I’ve had designers say they provide side bars, and top and bottom bars, fully lapped ‘preventing the cap from bursting out’, and just ignore this clause, while keeping the full strut capacity.
My view is not providing bursting reinforcement is not compliant with AS3600. But other codes, or ‘rational method of analysis’ could be used to justify?
How do other designers deal with the AS3600 requirement for bursting reinforcement?