MountainManMatt
Structural
- Jul 20, 2015
- 2
I have a question about elevated concrete slab design/detailing. Does the condition shown below meet the requirements of ACI? Can shear friction account for the shear transfer across the cracked joint? The goal is to assume a hinge for analysis purposes. Does the direct interaction of concrete below the reinforcing develop a negative moment? If so would the shear depth of the slab for shear capacity then be 1"?
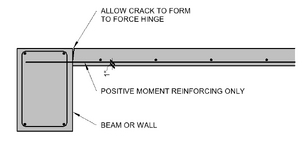
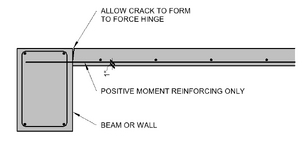