Shafty1
Mechanical
- Dec 27, 2018
- 3
Hello.
I have a pipe to clamp and am copying an existing design. It is an 'arch' design with 2 bolts. either side. see picture.
I'm checkign section for bending. at the smallest part of the arch (middle) . i am treating the arch as a beam with max moment as PL/4 (where P is 2 x the bolt force).
The current design is checked as failing (2000+ MPa) but i know it has been in use for AGES.
I am using the clamp load from tables for stainless bolts (lurbricated at about 56 kN). i suspect this high load is making the section fail. The pipe clamp is re-used, and hand tightened. over and over. What would be a reasonable bolt force? Or am i oversimplifying my asessment (or making fundamental error!!)?.
sketch below:
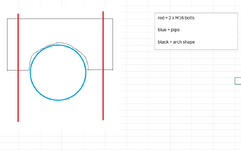
I have a pipe to clamp and am copying an existing design. It is an 'arch' design with 2 bolts. either side. see picture.
I'm checkign section for bending. at the smallest part of the arch (middle) . i am treating the arch as a beam with max moment as PL/4 (where P is 2 x the bolt force).
The current design is checked as failing (2000+ MPa) but i know it has been in use for AGES.
I am using the clamp load from tables for stainless bolts (lurbricated at about 56 kN). i suspect this high load is making the section fail. The pipe clamp is re-used, and hand tightened. over and over. What would be a reasonable bolt force? Or am i oversimplifying my asessment (or making fundamental error!!)?.
sketch below:
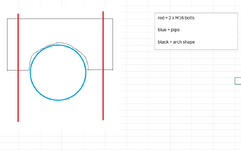