Hi All,
I'm designing a compressed air system that gets a connection from a Plant Air compressed system at 7 barG. I want to size the connecting piping in the way that it can provide enough flow and pressure to the all spray nozzles in attached. There are two types of nozzles (S1 and S2) need to be installed on the line. The line is approximately 5 meters long. S1 can flow 120 Nm3/hr and S2 can flow 50 Nm3/hr at 7 Barg.
I'm looking to find the related formula and calculations I need to do to ensure the pipe size is enough and I et enough flow and pressure at the last nozzle.
Thanks for your guidelines.
Please let me know what formulation and guidebook I can follow to resolve this for compressible fluid.
I'm designing a compressed air system that gets a connection from a Plant Air compressed system at 7 barG. I want to size the connecting piping in the way that it can provide enough flow and pressure to the all spray nozzles in attached. There are two types of nozzles (S1 and S2) need to be installed on the line. The line is approximately 5 meters long. S1 can flow 120 Nm3/hr and S2 can flow 50 Nm3/hr at 7 Barg.
I'm looking to find the related formula and calculations I need to do to ensure the pipe size is enough and I et enough flow and pressure at the last nozzle.
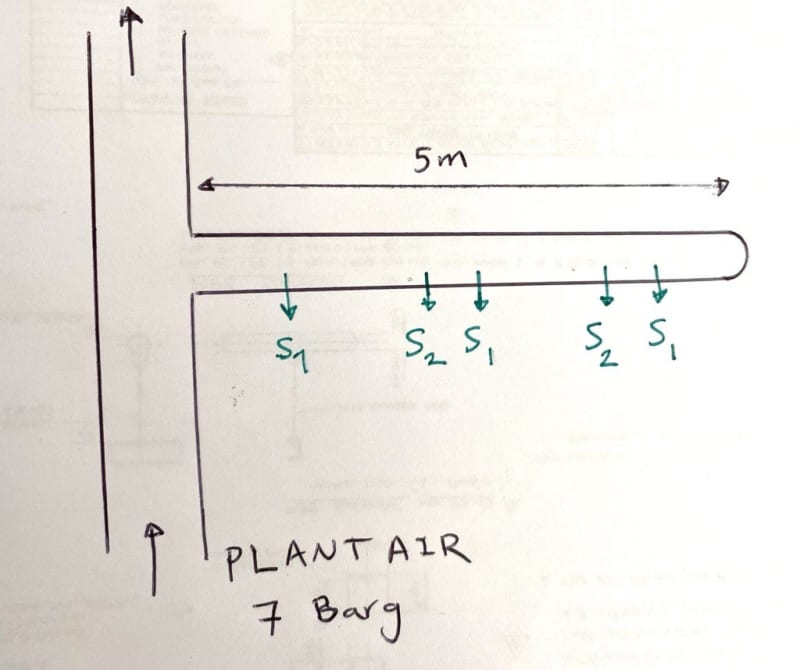
Thanks for your guidelines.
Please let me know what formulation and guidebook I can follow to resolve this for compressible fluid.