Hello All,
We are looking at a process line from the bottom of a pressure vessel to the suction side of a PD pump. Here's a snapshot of the stress model. 20" OD vessel, 6" piping, reduces down to 5" pump nozzle. You can see the vessel at the top anchored from it's support lugs, and the PD pump is modeled as a rigid element at the bottom. Looking at the suction flange on the PD pump, I have used API 676 allowable nozzle loads to evaluate whether the system is acceptable. I've got the whole length between the two yellow highlighted flanges to use for any kind of in-line flexibility element.
Operating Temp. - 415 deg. F
Operating Pressure - 0.1 PSIA
Design Temp. - 415 deg. F
Design Pressure - 150 PSIG
[li]A Tied Expansion Joint doesn't allow for axial thermal displacement and will overload the vessel and pump.[/li]
[li]An Untied Expansion Joint will create a pressure thrust in the design case that will overload the vessel and pump. I will see if the design pressure actually needs to be this high for this line, I suspect it's just from the fact that is a Class 150# system.[/li]
[li]A Pressure Balanced Joint should work, but I'd rather avoid a more complex piece of equipment than needed if possible.[/li]
Could a flex hose be used in this application if it can handle the design/operating temperatures, pressures, and displacements?
My main reason for asking this question is that it seems like a flex hose could be used sometimes when expansion joints are called out, but I'm not aware of all the possibilities of when to use one versus the other.
If anyone could provide more insight or resources into how to decide between expansion joints or Flex Hoses, I'd greatly appreciate the knowledge share.
Thanks!
We are looking at a process line from the bottom of a pressure vessel to the suction side of a PD pump. Here's a snapshot of the stress model. 20" OD vessel, 6" piping, reduces down to 5" pump nozzle. You can see the vessel at the top anchored from it's support lugs, and the PD pump is modeled as a rigid element at the bottom. Looking at the suction flange on the PD pump, I have used API 676 allowable nozzle loads to evaluate whether the system is acceptable. I've got the whole length between the two yellow highlighted flanges to use for any kind of in-line flexibility element.
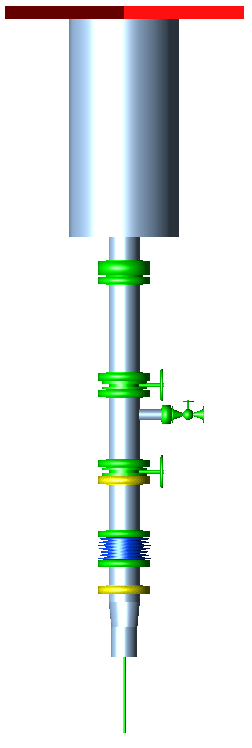
Operating Temp. - 415 deg. F
Operating Pressure - 0.1 PSIA
Design Temp. - 415 deg. F
Design Pressure - 150 PSIG
[li]A Tied Expansion Joint doesn't allow for axial thermal displacement and will overload the vessel and pump.[/li]
[li]An Untied Expansion Joint will create a pressure thrust in the design case that will overload the vessel and pump. I will see if the design pressure actually needs to be this high for this line, I suspect it's just from the fact that is a Class 150# system.[/li]
[li]A Pressure Balanced Joint should work, but I'd rather avoid a more complex piece of equipment than needed if possible.[/li]
Could a flex hose be used in this application if it can handle the design/operating temperatures, pressures, and displacements?
My main reason for asking this question is that it seems like a flex hose could be used sometimes when expansion joints are called out, but I'm not aware of all the possibilities of when to use one versus the other.
If anyone could provide more insight or resources into how to decide between expansion joints or Flex Hoses, I'd greatly appreciate the knowledge share.
Thanks!