BendingMoment123
Structural
Hi guys
I have an angle section welded to an end plate which is bolted to a steel beam below (Bolts are centred on the plate). Unfortunately, due to geometric constraints, this is the layout I have to work with.
How would you go about determining the bending capacity of the plate. From section B-B, would you calculate the plastic section modulus of the plate and the section modulus of the stiffeners, and then add them together for a combined moment capacity?
I have an angle section welded to an end plate which is bolted to a steel beam below (Bolts are centred on the plate). Unfortunately, due to geometric constraints, this is the layout I have to work with.
How would you go about determining the bending capacity of the plate. From section B-B, would you calculate the plastic section modulus of the plate and the section modulus of the stiffeners, and then add them together for a combined moment capacity?
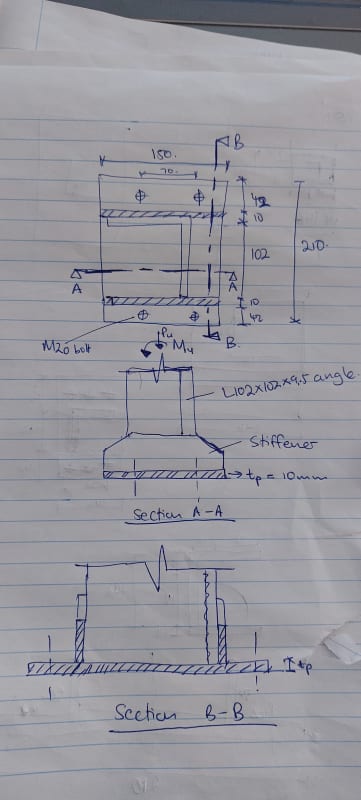