Hi guys,
I need some hint on how to verify the design of this jig attached here.
How to calculate weld sizes around the checker plate and SHS.
How to calculate the bending and shear stresses of the members around the checker plate and bottom 4 SHS as well.
Appreciate your suggestions.
Cheers
I need some hint on how to verify the design of this jig attached here.
How to calculate weld sizes around the checker plate and SHS.
How to calculate the bending and shear stresses of the members around the checker plate and bottom 4 SHS as well.
Appreciate your suggestions.
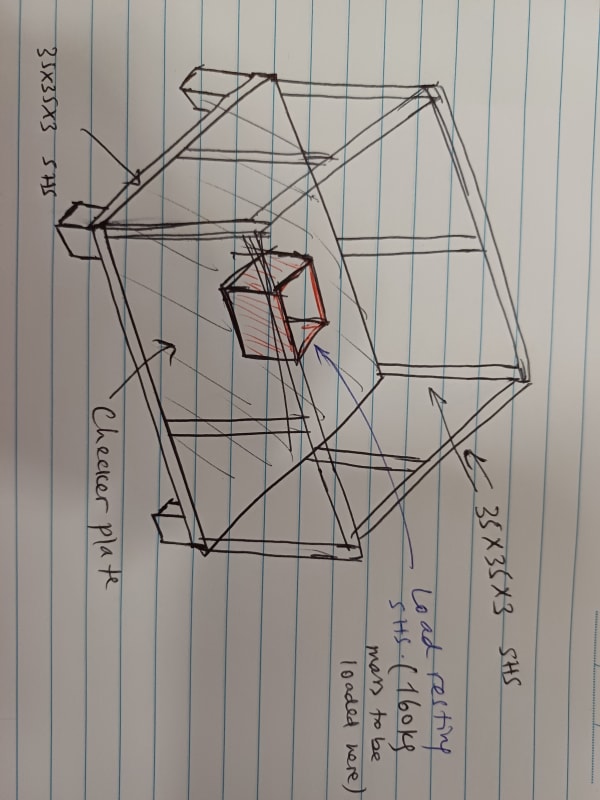
Cheers