RayJohnson2
Mechanical
Hi all,
I am considering the following design to seal a chamber (holding compressed air of 70 bar (~1000 psi)) using an o-ring.
I would like your advice on this.
See the attached sketch.
I have only sketched half the construction. It is pretty much symmetrical around the vertical axis, so imagine the same construction on the right side (not shown).
The chamber (inside diameter 9 mm) has a threaded rod inserted. Rod diameter 8 mm and screwthread M8 at both ends.
So the compressed air is in this circular 'gap' of 0.5 mm wide.
The chamber is sealed off at both ends with a nut and o-ring combination. The o-ring sits compressed in the groove in the nut.
Nothing spectacular there.
My question is about what could happen during assembly.
The nut is screwed on the threaded rod. At a certain point, the o-ring will start being compressed while the nut is still being rotated.
At that (short) time, the o-ring will get compressed while the nut is rotating, relative to the chamber.
I was wondering.. could the rotation and compressing at the same time cause a bad seal? I am not sure what the o-ring will do, due to the friction of the rotation of the nut.
Perhaps just being compressed (as I hope it will).
Maybe putting some grease in the groove might help to reduce friction on the o-ring to prevent it from being damaged by the rotation of the nut...
What do you all think? Am I worried for nothing..?
PS. Once assembled, this is a completely static construction. No movement at all.
Kind regards
Ray
I am considering the following design to seal a chamber (holding compressed air of 70 bar (~1000 psi)) using an o-ring.
I would like your advice on this.
See the attached sketch.
I have only sketched half the construction. It is pretty much symmetrical around the vertical axis, so imagine the same construction on the right side (not shown).
The chamber (inside diameter 9 mm) has a threaded rod inserted. Rod diameter 8 mm and screwthread M8 at both ends.
So the compressed air is in this circular 'gap' of 0.5 mm wide.
The chamber is sealed off at both ends with a nut and o-ring combination. The o-ring sits compressed in the groove in the nut.
Nothing spectacular there.
My question is about what could happen during assembly.
The nut is screwed on the threaded rod. At a certain point, the o-ring will start being compressed while the nut is still being rotated.
At that (short) time, the o-ring will get compressed while the nut is rotating, relative to the chamber.
I was wondering.. could the rotation and compressing at the same time cause a bad seal? I am not sure what the o-ring will do, due to the friction of the rotation of the nut.
Perhaps just being compressed (as I hope it will).
Maybe putting some grease in the groove might help to reduce friction on the o-ring to prevent it from being damaged by the rotation of the nut...
What do you all think? Am I worried for nothing..?
PS. Once assembled, this is a completely static construction. No movement at all.
Kind regards
Ray
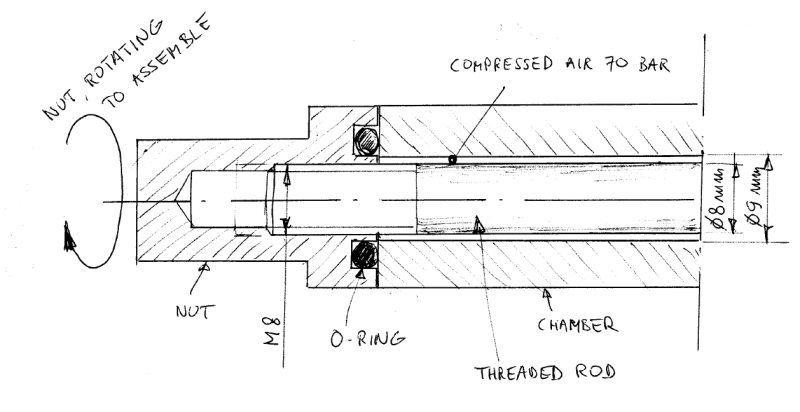