Mazda Carnage
Mechanical
- May 23, 2020
- 3
I am in the process of putting my 1988 Mazda 626GT in a new body.
Many things on the car are getting revamped.
The car has bolt on performance struts and 1" lowering springs, oversized sway bars and custom oversized poly link kits.
Strut tower bars, trailing axle bar, poly sway bar bushings. 4 new trailing axle arms, polyurethane trailing link bars, customized ball joint bolts...
I sandblasted 2 front control arms, pressed out the factory bushings, welded reinforcements for the link kit cups and welded steel loops for suspension travel limiting tie down straps for drag track use. Then installed 4 Nolathane polyurethane bushings.
The factory front control arm bushings are chemically bonded to the center sleeve, when the control arm is bolted to the crossmember at the ride height position (about 15degrees downward) the factory control arm bushings have a torsion resistance, it takes about 200 lbs pressure on old bushings to raise the control arm level with the crossmember so the factory front control arm bushings have a combined maximum resistance of 400-500 pounds. So if you remove the struts with springs the front control arm bushings will hold the front end of the car up and keep the crossmembers from hitting the ground.
The new Nolathane bushings use a greased center sleeve, the poly bushing is a bit longer than the center sleeve which would add some pressure to the center sleeve. But because it is greased at the center point the control arm will at some point move up or down on the center sleeve.
My concerns is that at the point the bushings move on the center sleeves, to the struts, springs and sway bar it would be as though the front end weight of the car has increased or the spring rate and swaybar size was lowered.
These are the bushings:
The Poly control arm bushings are meant to reduce torque steer by reducing control arm torsion under acceleration.
On my 1989 MX6 GT I used a bunch of old CV joint nuts that I ground down, put on both sides of the control arm bushings and pounded the control arms into the crossmembers. The nuts filled the gap between the control arm bushings rubber and crossmember, allowed up and down movement but 0 deflection, the car has no torque steer and rides great.
On the old 626GT the control arm bushings where a bit warn, I welded washers to the end of the control arm boxing in the bushing, the hole in the washer is the same size as the center sleeve and stops any torque deflection but allows up and down movement.
I ordered Polyurethane control arm bushings for both cars a few years back thinking it would stiffen up and down travel of the control arm and have 0 torque steer like both my cheap solutions to torque steer.
Now I am worried these Poly bushings might do the opposite of what I bought them for.
I contacted Nolathane with these concerns when I received the bushings years ago and also asked what boding agent they use to adhere the polyurethane to the outer sleeve but they did not reply.
I cannot find the polyurethane durometer rating but I would say they are high 70's-low 80's.
I told myself to quit worrying about this before I started assembling and welding the front control arms, after about 40hours work so far on the control arms and crossmembers and front sub frame getting them all to bare metal and ready to paint with POR15 and top coat, I still have to press in new ball joints and tack weld them, the Por15 cost 88$, the ball joints another 50$. Por15 is a pain in the ass to use, after bringing the part to bare metal it must be washed in expensive marine clean degreaser, rinsed, dried, sprayed with metal ready etching acid, rinsed, dried then painted.
My though was to try them with grease and if they suck try to clean them and bond the center sleeve in place, but that would be a pain and I'm not sure what Nolathane's "special squeak free grease" is made or of if it penetrates/conditions the polyurethane, can it be cleaned off 100%.
Before I go any farther with these control arms I really want another opinion.
Are my concerns about this design justified or ridiculous?
From my searching I have found similar (Not my make or model) polyurethane bushings with chemically bonded outer and inner sleeves. At what durometer would this be feasible and what bonding agent would be best for poly to mild steel?
I have many more control arms, 4moog double sleeved factory front control arm bushings would be about 120$, this time I would use the welded washer method (one at the front of the control arm and one at the back of the arm) then press in the bushings, this would allow the control arm to only move up and down and give more up and down resistance than worn out factory bushings but require a lot of work again and more money.
I live in Quebec Canada the roads are riddled with pot hole, ruts from heavy trucks during winter thaw and speed bumps. The cars weighs about 2650lbs, has 450 ft-lb instant wheel torque and is front wheel drive.
With all the work on the new body the only thing I am not working on is producing more power, I am adding piggy timing control over factory (modified) and better control over fuel, 3 stages of boost control (was 2) and 3 water meth stages (was two), everything else is handling, durability, braking and acceleration control.
This was a no budget build and managed 30psi boost on factory timing thanks to water/methanol injection, the MX6 has a laundry list of better performance parts on it and ready to install and is meant to be faster than the 626GT but the 626GT turned out to be faster than I expected any of my cars to be, never thought I would say this but it is fast enough.
Suggestions?
Many things on the car are getting revamped.
The car has bolt on performance struts and 1" lowering springs, oversized sway bars and custom oversized poly link kits.
Strut tower bars, trailing axle bar, poly sway bar bushings. 4 new trailing axle arms, polyurethane trailing link bars, customized ball joint bolts...
I sandblasted 2 front control arms, pressed out the factory bushings, welded reinforcements for the link kit cups and welded steel loops for suspension travel limiting tie down straps for drag track use. Then installed 4 Nolathane polyurethane bushings.
The factory front control arm bushings are chemically bonded to the center sleeve, when the control arm is bolted to the crossmember at the ride height position (about 15degrees downward) the factory control arm bushings have a torsion resistance, it takes about 200 lbs pressure on old bushings to raise the control arm level with the crossmember so the factory front control arm bushings have a combined maximum resistance of 400-500 pounds. So if you remove the struts with springs the front control arm bushings will hold the front end of the car up and keep the crossmembers from hitting the ground.
The new Nolathane bushings use a greased center sleeve, the poly bushing is a bit longer than the center sleeve which would add some pressure to the center sleeve. But because it is greased at the center point the control arm will at some point move up or down on the center sleeve.
My concerns is that at the point the bushings move on the center sleeves, to the struts, springs and sway bar it would be as though the front end weight of the car has increased or the spring rate and swaybar size was lowered.
These are the bushings:
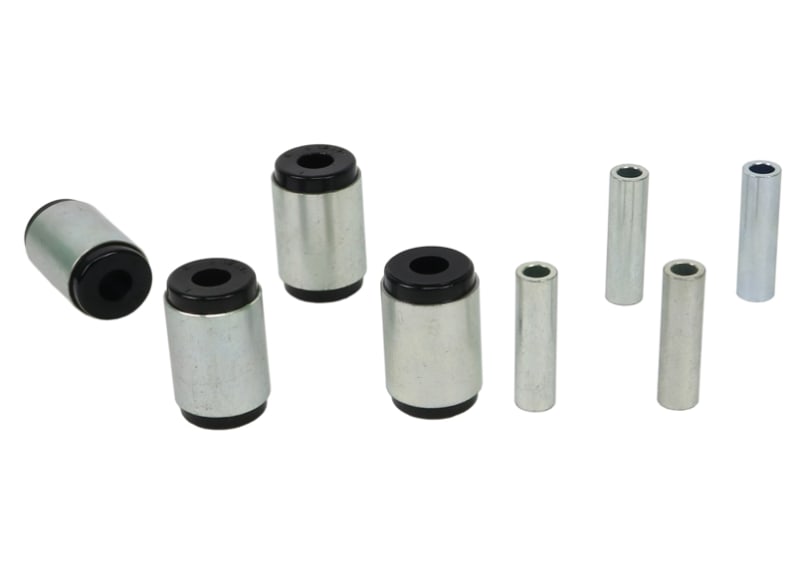
The Poly control arm bushings are meant to reduce torque steer by reducing control arm torsion under acceleration.
On my 1989 MX6 GT I used a bunch of old CV joint nuts that I ground down, put on both sides of the control arm bushings and pounded the control arms into the crossmembers. The nuts filled the gap between the control arm bushings rubber and crossmember, allowed up and down movement but 0 deflection, the car has no torque steer and rides great.
On the old 626GT the control arm bushings where a bit warn, I welded washers to the end of the control arm boxing in the bushing, the hole in the washer is the same size as the center sleeve and stops any torque deflection but allows up and down movement.
I ordered Polyurethane control arm bushings for both cars a few years back thinking it would stiffen up and down travel of the control arm and have 0 torque steer like both my cheap solutions to torque steer.
Now I am worried these Poly bushings might do the opposite of what I bought them for.
I contacted Nolathane with these concerns when I received the bushings years ago and also asked what boding agent they use to adhere the polyurethane to the outer sleeve but they did not reply.
I cannot find the polyurethane durometer rating but I would say they are high 70's-low 80's.
I told myself to quit worrying about this before I started assembling and welding the front control arms, after about 40hours work so far on the control arms and crossmembers and front sub frame getting them all to bare metal and ready to paint with POR15 and top coat, I still have to press in new ball joints and tack weld them, the Por15 cost 88$, the ball joints another 50$. Por15 is a pain in the ass to use, after bringing the part to bare metal it must be washed in expensive marine clean degreaser, rinsed, dried, sprayed with metal ready etching acid, rinsed, dried then painted.
My though was to try them with grease and if they suck try to clean them and bond the center sleeve in place, but that would be a pain and I'm not sure what Nolathane's "special squeak free grease" is made or of if it penetrates/conditions the polyurethane, can it be cleaned off 100%.
Before I go any farther with these control arms I really want another opinion.
Are my concerns about this design justified or ridiculous?
From my searching I have found similar (Not my make or model) polyurethane bushings with chemically bonded outer and inner sleeves. At what durometer would this be feasible and what bonding agent would be best for poly to mild steel?
I have many more control arms, 4moog double sleeved factory front control arm bushings would be about 120$, this time I would use the welded washer method (one at the front of the control arm and one at the back of the arm) then press in the bushings, this would allow the control arm to only move up and down and give more up and down resistance than worn out factory bushings but require a lot of work again and more money.
I live in Quebec Canada the roads are riddled with pot hole, ruts from heavy trucks during winter thaw and speed bumps. The cars weighs about 2650lbs, has 450 ft-lb instant wheel torque and is front wheel drive.
With all the work on the new body the only thing I am not working on is producing more power, I am adding piggy timing control over factory (modified) and better control over fuel, 3 stages of boost control (was 2) and 3 water meth stages (was two), everything else is handling, durability, braking and acceleration control.
This was a no budget build and managed 30psi boost on factory timing thanks to water/methanol injection, the MX6 has a laundry list of better performance parts on it and ready to install and is meant to be faster than the 626GT but the 626GT turned out to be faster than I expected any of my cars to be, never thought I would say this but it is fast enough.
Suggestions?