I'm adding pumping loss to my math models and have some questions for the experts.
My scavenge piston does nothing but draw ambient air in then push it through the main cylinder to flush exhaust gas and load the fresh air charge for intake (fuel is only added after both the intake and exhaust ports are closed).
I know the ambient conditions (at sea level and altitude), the air mass needs that needs to be moved, and the time over which it must be moved. From all of this, I calculate the required port area associated with a given pressure differential using the formulas below for choked and unchoked flow. I chose a conservative coefficient of discharge (C = 0.6) and low pressure differential (0.125 bar) when sizing the port area.
My questions are:
1) Since the air is flowing through two ports (intake and exhaust), do I have to double the differential ?
2) Is the pressure differential converted to isobaric work (Pressure * ΔVolume) the thermodynamic (sans friction) pumping loss ?
3) Isobaric work is positive as volume increases and negative as it decreases, so would the pumping loss be the difference ?
Thanks for any insight you can provide!
My scavenge piston does nothing but draw ambient air in then push it through the main cylinder to flush exhaust gas and load the fresh air charge for intake (fuel is only added after both the intake and exhaust ports are closed).
I know the ambient conditions (at sea level and altitude), the air mass needs that needs to be moved, and the time over which it must be moved. From all of this, I calculate the required port area associated with a given pressure differential using the formulas below for choked and unchoked flow. I chose a conservative coefficient of discharge (C = 0.6) and low pressure differential (0.125 bar) when sizing the port area.
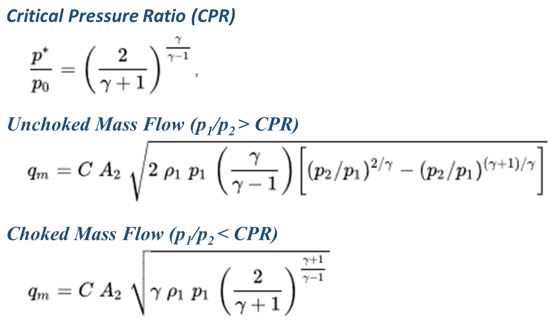
My questions are:
1) Since the air is flowing through two ports (intake and exhaust), do I have to double the differential ?
2) Is the pressure differential converted to isobaric work (Pressure * ΔVolume) the thermodynamic (sans friction) pumping loss ?
3) Isobaric work is positive as volume increases and negative as it decreases, so would the pumping loss be the difference ?
Thanks for any insight you can provide!