Hi everyone,
Is it possible to have a non-circular radial piston-type seal using o-rings? The Parker guide specifies minimum corner radii if I want to use a non-circular axial seal, but I don't see similar information for radial piston-type seals. If I were to take the minimum corner radii and try to implement similar, would the design seem feasible (so long as I follow compression criteria etc.) or is this likely to present problems? If so, any other solutions I should go for? Unfortunately we don't have the space for an axial seal, but could consider other seal types.
O-ring profile:
Side shot of groove (unfinished, just an example):
This lid would then fit into a flush box, with the radial o-ring providing a tight seal.
Thanks!
Is it possible to have a non-circular radial piston-type seal using o-rings? The Parker guide specifies minimum corner radii if I want to use a non-circular axial seal, but I don't see similar information for radial piston-type seals. If I were to take the minimum corner radii and try to implement similar, would the design seem feasible (so long as I follow compression criteria etc.) or is this likely to present problems? If so, any other solutions I should go for? Unfortunately we don't have the space for an axial seal, but could consider other seal types.
O-ring profile:
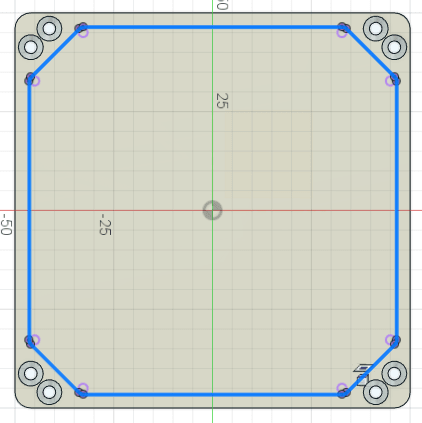
Side shot of groove (unfinished, just an example):
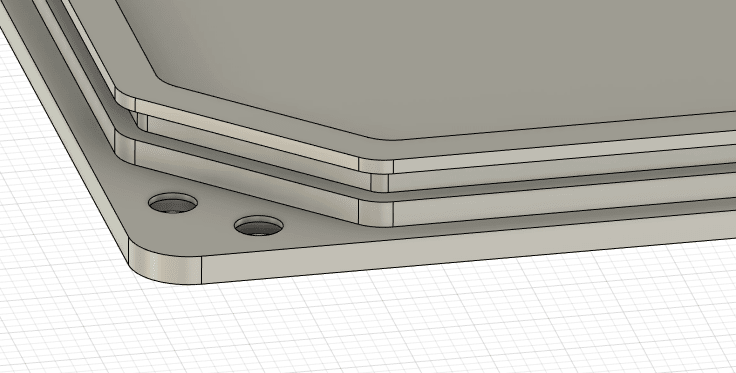
This lid would then fit into a flush box, with the radial o-ring providing a tight seal.
Thanks!