engineerlad123
Mechanical
- Apr 27, 2025
- 1
Hello,
I am evaluating running a line that connects to the discharge side of a pump where the pressure is approximately 800 psig. A block valve would be opened daily to fill from this line to an atmospheric vessel after the vessel goes through a restriction orifice. My question is that with the block valve closed the pressure on the other side of the restriction orifice before the block valve would be at the same static discharge pressure as before the orifice. Would there be a transient situation in this case where at the very beginning before steady state the block valve itself would be subject to that significant pressure drop? I'm evaluating this with a low vapor pressure liquid (MDEA) if that helps.
I guess I'm also just looking for good references/texts on this sort of design (taking a high pressure line and reducing it either for sampling or filling of a smaller system). This is more of an academic exercise unless I'm severely over-estimating the potential risk involved here as there are other options to work with that don't require pressures that high.
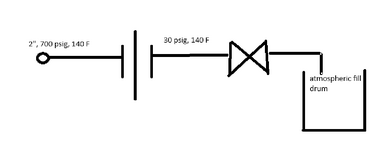
I am evaluating running a line that connects to the discharge side of a pump where the pressure is approximately 800 psig. A block valve would be opened daily to fill from this line to an atmospheric vessel after the vessel goes through a restriction orifice. My question is that with the block valve closed the pressure on the other side of the restriction orifice before the block valve would be at the same static discharge pressure as before the orifice. Would there be a transient situation in this case where at the very beginning before steady state the block valve itself would be subject to that significant pressure drop? I'm evaluating this with a low vapor pressure liquid (MDEA) if that helps.
I guess I'm also just looking for good references/texts on this sort of design (taking a high pressure line and reducing it either for sampling or filling of a smaller system). This is more of an academic exercise unless I'm severely over-estimating the potential risk involved here as there are other options to work with that don't require pressures that high.
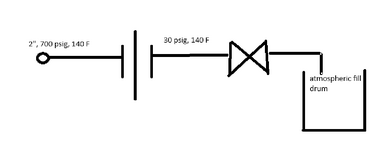