v6racer
Electrical
- Sep 30, 2005
- 13
Hi, to start my degree is in micro electronics so power distribution isn't my strong suit despite working through college as a journeyman. The journeyman stuff was why I have been asked to look into this.
Anyway, on the 480 volt power to some of our crystal furnaces we have some regularly occurring transients that our process guys insist are affecting yield. These are +- 1% which is well within the spec for incoming power. I have confirmed that it is most likely incoming power as I have seen the pattern on two different substations. Supposedly we do not have automatic power factor correction or on load tap changers and can't say those would match the data. Any idea what would cause the changes shown in the pic below?
Since the process engineers insist it affect their yield I will have to mitigate these changes. I am thinking either a rotatory or battery UPS. Can you suggest anything else I might want to look into?
Anyway, on the 480 volt power to some of our crystal furnaces we have some regularly occurring transients that our process guys insist are affecting yield. These are +- 1% which is well within the spec for incoming power. I have confirmed that it is most likely incoming power as I have seen the pattern on two different substations. Supposedly we do not have automatic power factor correction or on load tap changers and can't say those would match the data. Any idea what would cause the changes shown in the pic below?
Since the process engineers insist it affect their yield I will have to mitigate these changes. I am thinking either a rotatory or battery UPS. Can you suggest anything else I might want to look into?
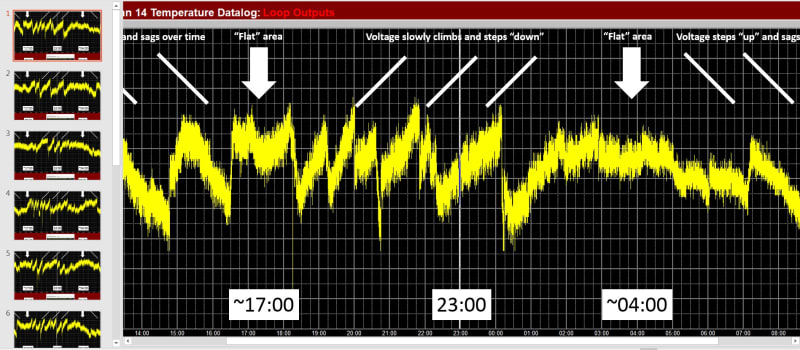