LonelyDeer
Structural
- Dec 30, 2015
- 13
Hello.
I've tried to find an answer during hard internet search (without result). I hope you'll help me.
Input:
1.Pedestrian bridge
2. Soil conditions ( 1m of sand, 4-5m of expansive clay with high expansive strain, weathered rock - argillite),
3. Therefore - pile abutment (flood is common thing in this place, so clay will expand -> we need to go further to the rock)
Design process:
First idea - boring piles d=600-800mm was banned ( too expensive, uneducated workers (Eastern Europe) + too hard to control pile quality). Second idea - precast concrete driven piles (rectangular 350x350mm). But here we have a problem.
Rock layer have rather steep angle, so we can't guarantee reliability of pile's end bearing, because during driving pile's shoe can slip down and pile will go out of it's normal way.
Things may go like here (except welding joints, our pile is solid - one section)[Pile Design and Construction Practice, sixth ed., Tomlinson, Woodward].
Third idea - drive pile (rectangular) in pre-bored hole (d=400mm - bore 0.5-1m in rock) and then put a low-class concrete between pile and soil.
Or fourth idea - drive pile (rectangular) in pre-bored hole (d=300mm - bore 0.5-1m in rock). I'm afraid that in that case pile's end won't completely enter in rock or corners of pile's end will shear, but on the other hand rock is rather weathered.
And here is my question. Does anybody knows anything about such thing in practice (book, article)? Or some help in terminology, how this method called in world practice? Or maybe somebody can tell me about proper way to create a reliable contact between rock and pile.
Thank you.
I've tried to find an answer during hard internet search (without result). I hope you'll help me.
Input:
1.Pedestrian bridge
2. Soil conditions ( 1m of sand, 4-5m of expansive clay with high expansive strain, weathered rock - argillite),
3. Therefore - pile abutment (flood is common thing in this place, so clay will expand -> we need to go further to the rock)
Design process:
First idea - boring piles d=600-800mm was banned ( too expensive, uneducated workers (Eastern Europe) + too hard to control pile quality). Second idea - precast concrete driven piles (rectangular 350x350mm). But here we have a problem.
Rock layer have rather steep angle, so we can't guarantee reliability of pile's end bearing, because during driving pile's shoe can slip down and pile will go out of it's normal way.
Things may go like here (except welding joints, our pile is solid - one section)[Pile Design and Construction Practice, sixth ed., Tomlinson, Woodward].
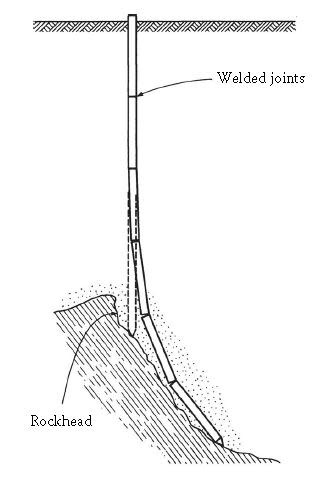
Third idea - drive pile (rectangular) in pre-bored hole (d=400mm - bore 0.5-1m in rock) and then put a low-class concrete between pile and soil.
Or fourth idea - drive pile (rectangular) in pre-bored hole (d=300mm - bore 0.5-1m in rock). I'm afraid that in that case pile's end won't completely enter in rock or corners of pile's end will shear, but on the other hand rock is rather weathered.
And here is my question. Does anybody knows anything about such thing in practice (book, article)? Or some help in terminology, how this method called in world practice? Or maybe somebody can tell me about proper way to create a reliable contact between rock and pile.
Thank you.