JohnRwals
Structural
- Jul 8, 2020
- 151
Hello!
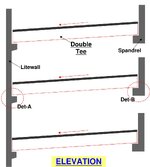
These questions are related with precast production efficiency and member design detail.
Double tee floors are sloped everywhere in the precast concrete parking structures;
let's assume 60ft long 12DT34 and typical floor slope 2% for drainage.
1. Is it really necessary to make double tees with (1/2") batter like Double Tee-1
instead of straight vertical ends like Double Tee-2? (Typical end joint width is 3/4".)
This makes end formwork complicated, which will reduce production productivity.
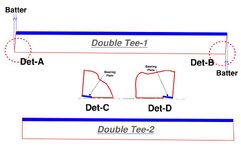
2. Double Tee-1 shows bearing plates are flush with stem surface, which is good for production efficiency.
Is it really necessary to make bearing plates tilted like Det-C, D to make uniform bearing?
Does Double Tee-2 production method which will cause non-uniform bearing stress really matter?
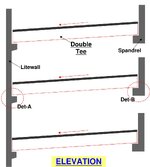
These questions are related with precast production efficiency and member design detail.
Double tee floors are sloped everywhere in the precast concrete parking structures;
let's assume 60ft long 12DT34 and typical floor slope 2% for drainage.
1. Is it really necessary to make double tees with (1/2") batter like Double Tee-1
instead of straight vertical ends like Double Tee-2? (Typical end joint width is 3/4".)
This makes end formwork complicated, which will reduce production productivity.
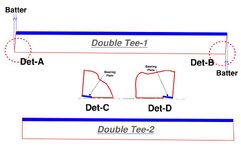
2. Double Tee-1 shows bearing plates are flush with stem surface, which is good for production efficiency.
Is it really necessary to make bearing plates tilted like Det-C, D to make uniform bearing?
Does Double Tee-2 production method which will cause non-uniform bearing stress really matter?