bowlingdanish
Structural
- Jan 22, 2015
- 87
Hello
Might be a bit of an odd question but I can't seem to find much online so here we go; I am working on an office building where the contractor is looking to use precast elements for everything. So precast floors spanning to precast beams to precast columns, the whole deal.
The building has extremely long spans and at the exterior the primary beams have to cantilever out a long way past the inset columns to support the floor. Since the spans are so long, we need to prestress the concrete to keep deflections in check with a reasonable beam depth. Which is all good for single span module elements, but I'm having a hard time getting my head around how we can prestress a precast multi span cantilever beam.
Pretensioning wouldn't make sense as the strands need to be straight, so the moment reversal could end up reducing capacity and increasing deflection in the cantilever. Unless... you somehow calibrate strand location at a section depth that would counter the expected deformed shape of the cantilever (i.e based on cantilever/backspan ratio)? Seems far fetched.
Post-tensioning the beams could also be an option, as you could drape the tendons to the moment distribution. But then, if it's tensioned in a factory setting, there'd be no supports to constrain movement (i.e no hyperstatic forces), so the beam would still want to deflect up as below;
In both pre- or post- tensioning, after tensioning the concrete, the relative vertical level of beam soffit at the column locations would not be the same (as they would for single span). Which seems like a nightmare with tolerances and installation specification.
Am I missing something/is this even possible?
Might be a bit of an odd question but I can't seem to find much online so here we go; I am working on an office building where the contractor is looking to use precast elements for everything. So precast floors spanning to precast beams to precast columns, the whole deal.
The building has extremely long spans and at the exterior the primary beams have to cantilever out a long way past the inset columns to support the floor. Since the spans are so long, we need to prestress the concrete to keep deflections in check with a reasonable beam depth. Which is all good for single span module elements, but I'm having a hard time getting my head around how we can prestress a precast multi span cantilever beam.
Pretensioning wouldn't make sense as the strands need to be straight, so the moment reversal could end up reducing capacity and increasing deflection in the cantilever. Unless... you somehow calibrate strand location at a section depth that would counter the expected deformed shape of the cantilever (i.e based on cantilever/backspan ratio)? Seems far fetched.
Post-tensioning the beams could also be an option, as you could drape the tendons to the moment distribution. But then, if it's tensioned in a factory setting, there'd be no supports to constrain movement (i.e no hyperstatic forces), so the beam would still want to deflect up as below;
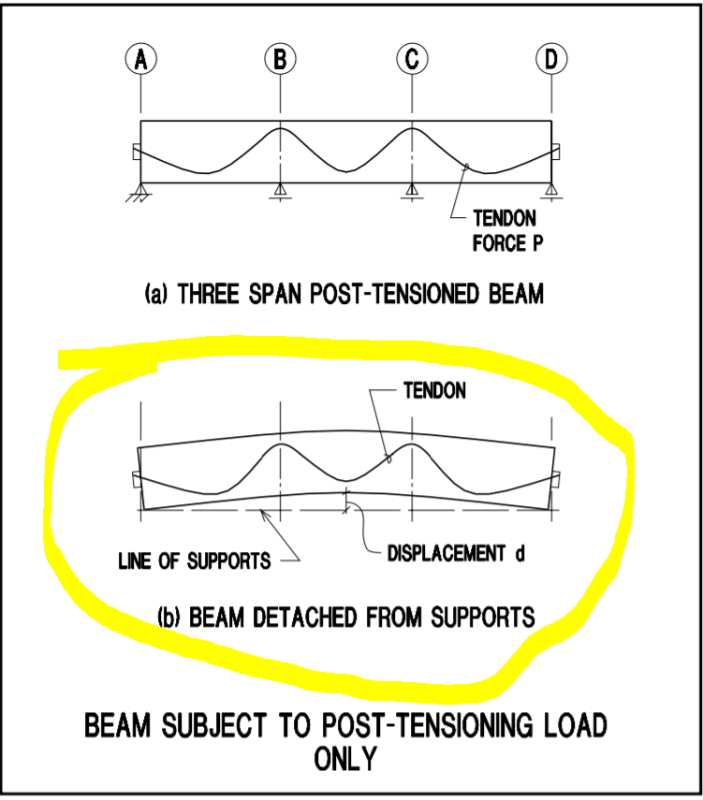
In both pre- or post- tensioning, after tensioning the concrete, the relative vertical level of beam soffit at the column locations would not be the same (as they would for single span). Which seems like a nightmare with tolerances and installation specification.
Am I missing something/is this even possible?