I have a situation where a short (~1.2 m) precast retaining wall would need to be installed on a cast in-situ footing. For various reasons that I won't go into, a cast in-situ wall may not be doable in this case.
I am exploring various options, including:
A) One similar to the picture below with reinforcement starter bars that slot into metal PT ducts and then grouted. Note that I would have two layers of reinforcement in the precast wall, with a single row of bars forming the connection.
B) Threaded rods projecting from the footing instead of reinforcement, slotted through the full height of the wall and bolted at the top, then the duct and recess grouted.
C) Same as B) but with 1030 Grade stress bars and some post-tensioning applied.
What is the performance of this type of precast wall connection for out-of-plane bending? Strength is no concern, as this will require relatively little reinforcement. My main concern would be that a fairly wide crack would open up at the base of the wall and cause a potential durability problem.
AS5100.5 (the code I need to use) states that walls >150 mm thick need to have 2 layers of reinforcement (one at each face). In my case, this would be satisfied within the precast wall itself, but not in the plane of the connection. Is this allowable?
Regarding the spacing of the bars forming the connection, am I also forced to stick to the 300 mm limit for walls? With a 2.4 m long wall segment, would it be particularly onerous to have to align 8 bars to slot into the wall?
I am exploring various options, including:
A) One similar to the picture below with reinforcement starter bars that slot into metal PT ducts and then grouted. Note that I would have two layers of reinforcement in the precast wall, with a single row of bars forming the connection.
B) Threaded rods projecting from the footing instead of reinforcement, slotted through the full height of the wall and bolted at the top, then the duct and recess grouted.
C) Same as B) but with 1030 Grade stress bars and some post-tensioning applied.
What is the performance of this type of precast wall connection for out-of-plane bending? Strength is no concern, as this will require relatively little reinforcement. My main concern would be that a fairly wide crack would open up at the base of the wall and cause a potential durability problem.
AS5100.5 (the code I need to use) states that walls >150 mm thick need to have 2 layers of reinforcement (one at each face). In my case, this would be satisfied within the precast wall itself, but not in the plane of the connection. Is this allowable?
Regarding the spacing of the bars forming the connection, am I also forced to stick to the 300 mm limit for walls? With a 2.4 m long wall segment, would it be particularly onerous to have to align 8 bars to slot into the wall?
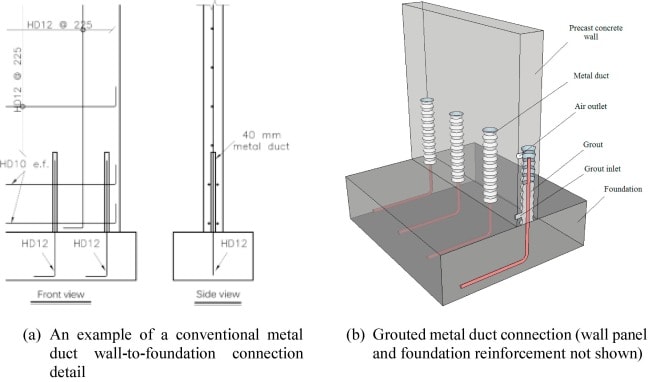