Brent Boisvenue
Mining
- Mar 11, 2021
- 16
Hi everyone,
I'm designing a type of ram for a high temperature furnace application requiring linear guidance. I have two linear guides on the top of the machine and a "push rod" at the bottom connected to a pneumatic cylinder (see attached image). I have guide tubes (grey) projecting out the back of the mechanism, housing high temperature Thermalloy bushings. The guide rods (green) project through the flange and into the furnace and are supported on the back side using the guide tubes that are mounted to a 1" flange to the burner.
I have three methods I'm considering for attaching the guide tubes to the flange:
[li] Threaded connection with shoulder (current design shown in screenshot)[/li]
[li] Press-fit[/li]
[li] Slip-fit hole with bevel weld ground flush on back side[/li]
Given that this is a linear guidance application, I'm looking for something that can provide decent perpendicularity to ensure alignment, although I've build in a decent amount of slop since the application doesn't require any precision. My first instinct was to use a threaded and shouldered connection (shown in the attached screenshot). However, one of my colleagues is a bit concerned that I won't get the requisite perpendicularity from the threaded connection.
Any recommendations?
I'm designing a type of ram for a high temperature furnace application requiring linear guidance. I have two linear guides on the top of the machine and a "push rod" at the bottom connected to a pneumatic cylinder (see attached image). I have guide tubes (grey) projecting out the back of the mechanism, housing high temperature Thermalloy bushings. The guide rods (green) project through the flange and into the furnace and are supported on the back side using the guide tubes that are mounted to a 1" flange to the burner.
I have three methods I'm considering for attaching the guide tubes to the flange:
[li] Threaded connection with shoulder (current design shown in screenshot)[/li]
[li] Press-fit[/li]
[li] Slip-fit hole with bevel weld ground flush on back side[/li]
Given that this is a linear guidance application, I'm looking for something that can provide decent perpendicularity to ensure alignment, although I've build in a decent amount of slop since the application doesn't require any precision. My first instinct was to use a threaded and shouldered connection (shown in the attached screenshot). However, one of my colleagues is a bit concerned that I won't get the requisite perpendicularity from the threaded connection.
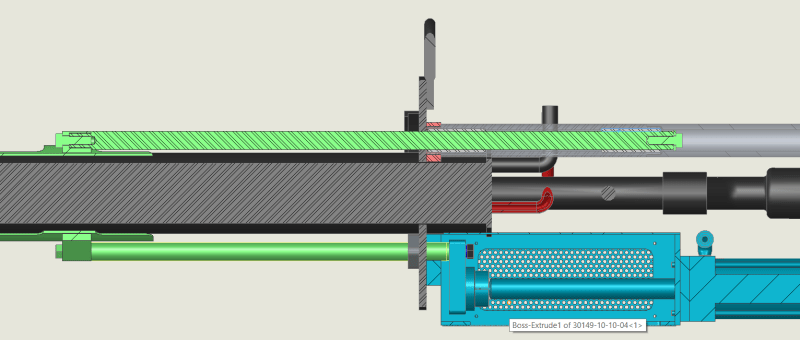
Any recommendations?