Hi,
I am trying to understand what a certian pressure at the bottom of a tank would be.
I have attached a drawing trying to sketch the problem.
The pump is pumping water in at at the bottom with a fixed volume/hr and pressure .
The water then travels through some biomedia which results in a pressure loss Y, this loss increases to pressure loss Z over time but let us assume a pressure of X.
And the of course the water column with a pressure of W.
What would the pressure transducere show at a given time?
Thanks
I am trying to understand what a certian pressure at the bottom of a tank would be.
I have attached a drawing trying to sketch the problem.
The pump is pumping water in at at the bottom with a fixed volume/hr and pressure .
The water then travels through some biomedia which results in a pressure loss Y, this loss increases to pressure loss Z over time but let us assume a pressure of X.
And the of course the water column with a pressure of W.
What would the pressure transducere show at a given time?
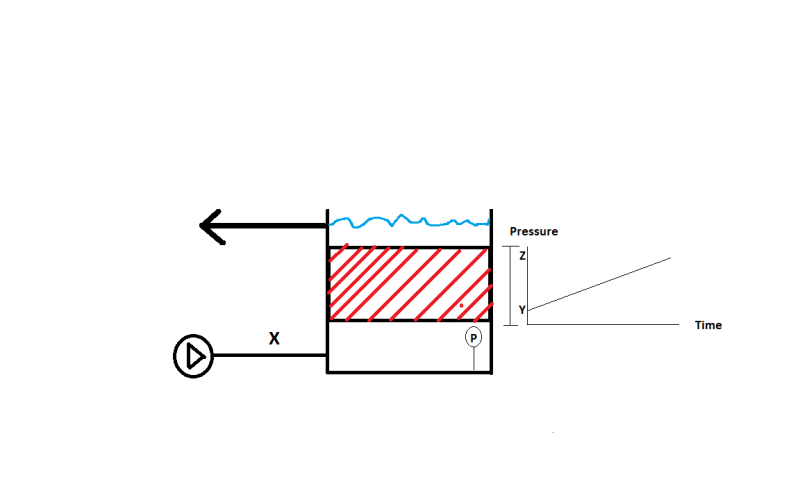
Thanks