MntReliabilityEng
Mechanical
Hey everyone,
I am working on a pressure cast system that is running highly abrasive pottery slip and valves are failing on a biweekly basis.
Here is a simple drawing of one of the 20 stems on the system:
We are currently running 3/4" actuated ball valves with reinforced Teflon seats made by Bi-Torq for both the fill and drain. The system starts by building 160psi, the fill valve opens, and injects the slip into the mold. After the mold is cast, the fill valve closes and the drain valve opens to atmospheric pressure. Its good to note that these ball valves are not used as flow controllers so its either 100% open or 100% closed. The problem we are having seems to be attributed to the drain valves opening under full pressure to ATM. The valve seats are eroding and the slip is able to bypass during the fill cycle causing a loss of pressure. I have theorized a few ways to reduce the amount of wear but I am not an expert so I figured I would come here for advice. My thought is that they could switch from 3/4" to a 1" ball valve in that section to create an expansion chamber which would slow the flow velocity past the valve by 44% while maintaining the same flow rate. They have also considered switching to a ceramic ball and valve seat but its not offered by Bi-Torq so we might need to use a different actuator. I have even looked into switching to a pneumatic actuated gate/knife valve but I don't know if that would be any better. What are your thoughts?
Joe-
I am working on a pressure cast system that is running highly abrasive pottery slip and valves are failing on a biweekly basis.
Here is a simple drawing of one of the 20 stems on the system:
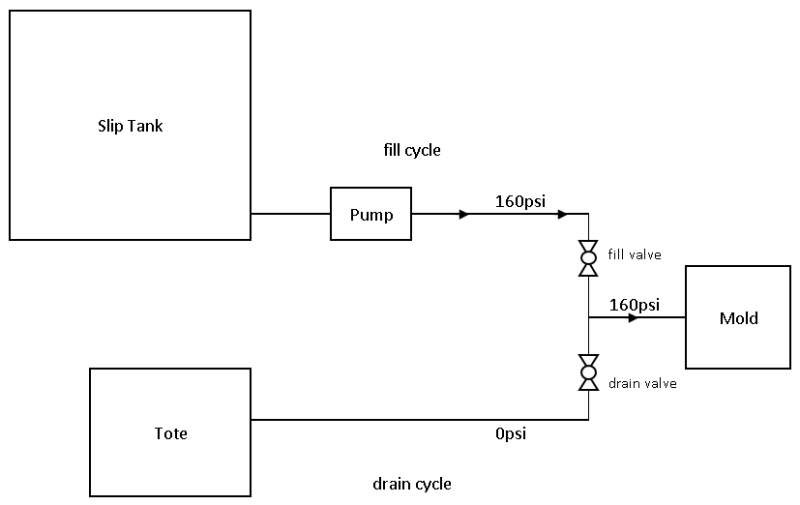
We are currently running 3/4" actuated ball valves with reinforced Teflon seats made by Bi-Torq for both the fill and drain. The system starts by building 160psi, the fill valve opens, and injects the slip into the mold. After the mold is cast, the fill valve closes and the drain valve opens to atmospheric pressure. Its good to note that these ball valves are not used as flow controllers so its either 100% open or 100% closed. The problem we are having seems to be attributed to the drain valves opening under full pressure to ATM. The valve seats are eroding and the slip is able to bypass during the fill cycle causing a loss of pressure. I have theorized a few ways to reduce the amount of wear but I am not an expert so I figured I would come here for advice. My thought is that they could switch from 3/4" to a 1" ball valve in that section to create an expansion chamber which would slow the flow velocity past the valve by 44% while maintaining the same flow rate. They have also considered switching to a ceramic ball and valve seat but its not offered by Bi-Torq so we might need to use a different actuator. I have even looked into switching to a pneumatic actuated gate/knife valve but I don't know if that would be any better. What are your thoughts?
Joe-