rollingcloud
Aerospace
This is for pressure testing on a pressure relief valve. The aim is to adjust the inlet pressure from 0.00 to 150.00 psig. However, we are experiencing jumps in the pressure readings, typically in increments of 5-10 psig—for example, jumping directly from 110 to 120 psig. Ideally, the pressure should increase in finer increments, like 111, 112, 113, etc. Our testing setup, as designed by a previous engineer, utilizes the TESCOM 44-1800 series. This regulator is capable of handling a maximum inlet pressure of 6000 psig and an outlet pressure range of 0-2500 psig. Since we are only operating within a 0–150 psig range, the 0-2500 psig capability appears to be excessive to me. Perhaps a regulator of the same type but designed for a lower pressure range would provide better resolution/control?
The current setup from our supplier includes a pressure regulator on top of the tank and a needle valve before the inlet. However, this arrangement is resulting in pressure jumps of 5-10 psig during testing when the operator adjusts the pressure regulator's knob.
The current setup from our supplier includes a pressure regulator on top of the tank and a needle valve before the inlet. However, this arrangement is resulting in pressure jumps of 5-10 psig during testing when the operator adjusts the pressure regulator's knob.
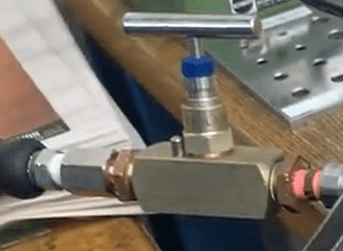
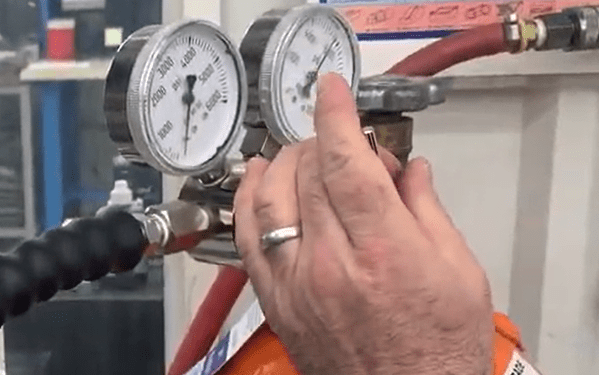