Leonardop318
Mechanical
Hi everyone,
I'm working on a project where a have to design a closed-loop calibration rig that has to work like this:
1. Circulate (1-2m3/h) a fluid at 20°C and 10 bar.
2. Take the readings from the meters.
3. Raise pressure to 30bar, take readings, and then to 50 and 80 bar
4. Raise temperature to 60°C and start again from 10 to 80 bar.
I asked in a previous post and I was told I could use a gear pump to make flow the fluid, and an additional small pump to add/extract fluid in order to increase or decrease pressure.
Do you guys know what kind of pump would do the job?
What else would I need to consider to make it work?
Do you have any additional suggestion?
Thanks in advance.
I'm working on a project where a have to design a closed-loop calibration rig that has to work like this:
1. Circulate (1-2m3/h) a fluid at 20°C and 10 bar.
2. Take the readings from the meters.
3. Raise pressure to 30bar, take readings, and then to 50 and 80 bar
4. Raise temperature to 60°C and start again from 10 to 80 bar.
I asked in a previous post and I was told I could use a gear pump to make flow the fluid, and an additional small pump to add/extract fluid in order to increase or decrease pressure.
Do you guys know what kind of pump would do the job?
What else would I need to consider to make it work?
Do you have any additional suggestion?
Thanks in advance.
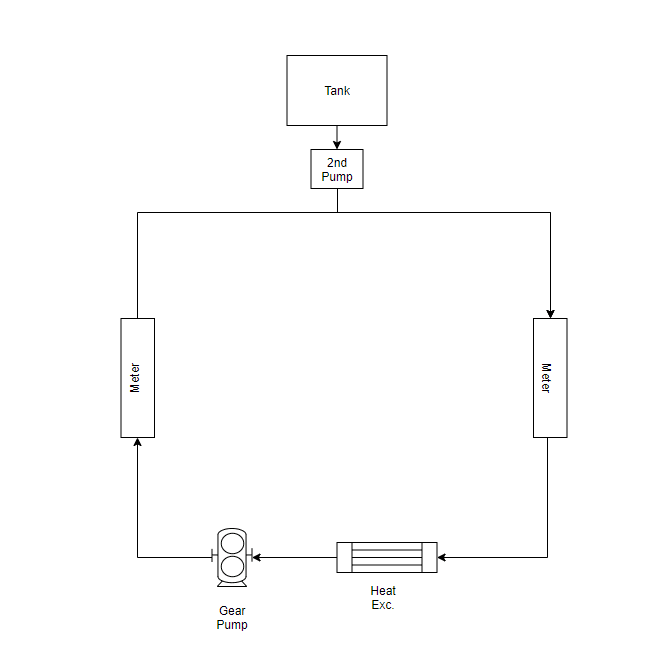