Hi All
I am checking the requirement if there is a need for Pressure/vacuum relief valve on a slurry tank.
API650 design check, internal pressure was calculated at 8.1kPa. I believe API650 allow for up to 6.9kPa.
However, there is tank overflow to a seal pot downstream (built to AS1210),
which probably mitigate the overpressure and vacuum effect in the tank.
I wonder if a pressure/vacuum relief valve is still required?
Previous experience with tanks - they have their own relief valve. But not this one.
Tank has a frangible roof to shell connection. Would it make a difference if it is not, in this case?
I am checking the requirement if there is a need for Pressure/vacuum relief valve on a slurry tank.
API650 design check, internal pressure was calculated at 8.1kPa. I believe API650 allow for up to 6.9kPa.
However, there is tank overflow to a seal pot downstream (built to AS1210),
which probably mitigate the overpressure and vacuum effect in the tank.
I wonder if a pressure/vacuum relief valve is still required?
Previous experience with tanks - they have their own relief valve. But not this one.
Tank has a frangible roof to shell connection. Would it make a difference if it is not, in this case?
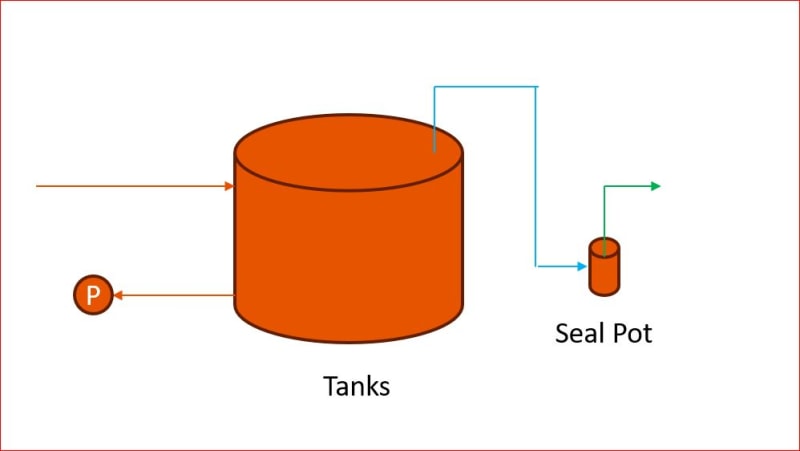