Hi,
Appreciate suggestions regarding the below case.
The liquid outlet from the separator is saturated, that means any reduction in pressure will result in a slight evaporation of the liquid and the formation of gas bubbles. In the attached scenario, the level control valve induces pressure reduction, leading to the creation of gas bubbles, a phenomenon known as "flashing," which can adversely affect the control valve, potentially causing erosion and damaging it. In such cases, how can we prevent flashing, or what are the typical ways to handle this situation?
Appreciate suggestions regarding the below case.
The liquid outlet from the separator is saturated, that means any reduction in pressure will result in a slight evaporation of the liquid and the formation of gas bubbles. In the attached scenario, the level control valve induces pressure reduction, leading to the creation of gas bubbles, a phenomenon known as "flashing," which can adversely affect the control valve, potentially causing erosion and damaging it. In such cases, how can we prevent flashing, or what are the typical ways to handle this situation?
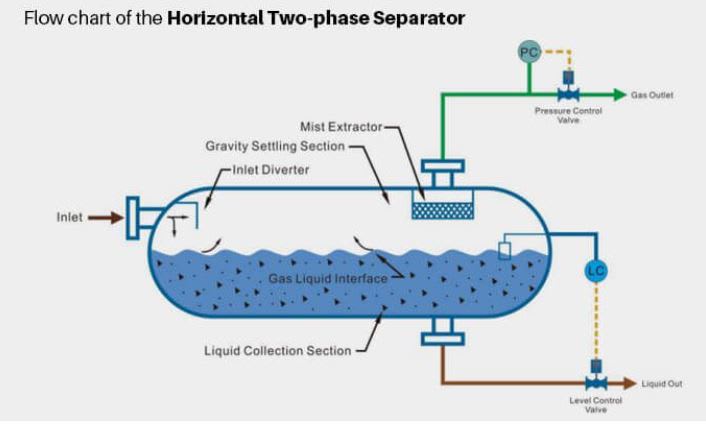