I am doing simulations of a cyclic pressure applied to a surface of a circle. The model is a quarter model of a circle, with the pressure applied in the z-direction, the thickness is 0.4 mm and diameter 20 mm, where the material is a user subroutine of a hyperelastic matrix-fibre composite (neo-hookean matrix and an exponential model for the fibres).
The UMAT calculates a plastic stress specifically in the neo-hookean matrix component, according to the peak strain at each cycle, in order to produce a permanent set (i.e. unrecoverable strain) when unloaded. The simulations break down after a few pressure loading cycles, with no obvious reason why- there aren't any major stress/strain concentrations, and the permanent set values are increasing linearly with each cycle. The message file error is just that the solution appears to be diverging. The simulations converge for lower levels of plastic stress but the model inputs are increased to produce more plastic stress per cycle, the simulation breaks down. It appears that its the levels of plastic stress that are causing problems in the solution converging.
Can anyone help with this or suggest why the simulation might be breaking down? Thank you in advance.
The UMAT calculates a plastic stress specifically in the neo-hookean matrix component, according to the peak strain at each cycle, in order to produce a permanent set (i.e. unrecoverable strain) when unloaded. The simulations break down after a few pressure loading cycles, with no obvious reason why- there aren't any major stress/strain concentrations, and the permanent set values are increasing linearly with each cycle. The message file error is just that the solution appears to be diverging. The simulations converge for lower levels of plastic stress but the model inputs are increased to produce more plastic stress per cycle, the simulation breaks down. It appears that its the levels of plastic stress that are causing problems in the solution converging.
Can anyone help with this or suggest why the simulation might be breaking down? Thank you in advance.
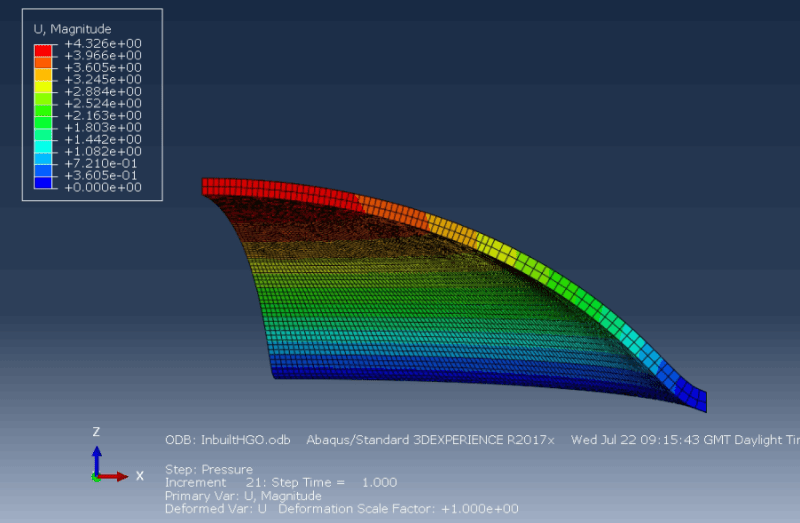