Jack Nicholson
Chemical
Dear all.
HELLO.
I have an is
sue.
As illustrated on attached picture, liquid ethane is warmed and by thermosyphon mechanism, two phase ethane goes back to circulation drum.
Unfortunately U-type piping right after cold box is done, so it has a negative effect on thermosyphon moving and during decreasing flow of hot stream, thermosyphon flow would be stopped or oscillated.
One solution is to introduce a 1 inch pipe containing vapor ethane to reinforce thermosyphon flow during low heat transfer on cold box. What's your Idea?
HELLO.
I have an is
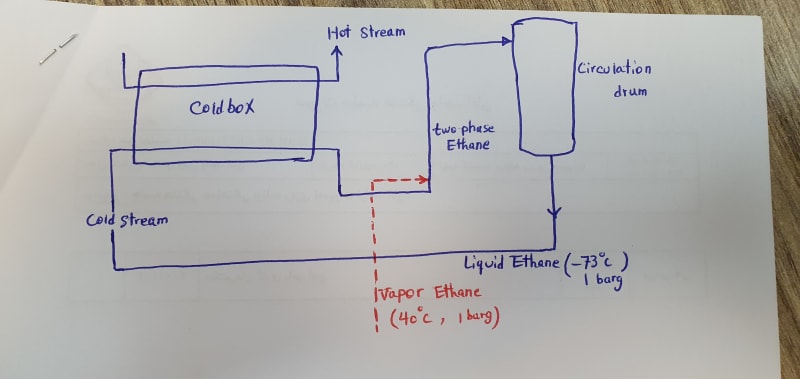
As illustrated on attached picture, liquid ethane is warmed and by thermosyphon mechanism, two phase ethane goes back to circulation drum.
Unfortunately U-type piping right after cold box is done, so it has a negative effect on thermosyphon moving and during decreasing flow of hot stream, thermosyphon flow would be stopped or oscillated.
One solution is to introduce a 1 inch pipe containing vapor ethane to reinforce thermosyphon flow during low heat transfer on cold box. What's your Idea?