Algirdas13
Mechanical
Hey everyone,
I'm facing a problem with non-linear analysis using shell elements. The software is Nastran in CAD (Autodesk Inventor Add-in).
I did a simple analysis of the lifting lug by using 3D solid elements (parabolic order) and bi-linear material (LGDISP is on). The model performed pretty well and managed to reach the plateau (plastic deformation).
After that I tried to do the exactly same simulation but using 2D shell elements (parabolic order), bi-linear material (LGDISP is on). In such case during the analysis a plateau (plastic deformation) wasn't reached. Solver managed only capture the elastic-plastic transition and then stopped because of calculations resulting in divergency.
For both analysis I used same parameters, material properties and force. For 2D calculation I also tried to increase number of increments.
Maybe someone could help me out to figure out or share some insights what I did wrong in analysis where I used shell elements?
P.S. these calculations are not meant to determine capacity of lifting lug but rather to learn how to perform a non-linear analysis and see the correlation regarding the hand calculations.
Shell setup:
Solid setup:
I'm facing a problem with non-linear analysis using shell elements. The software is Nastran in CAD (Autodesk Inventor Add-in).
I did a simple analysis of the lifting lug by using 3D solid elements (parabolic order) and bi-linear material (LGDISP is on). The model performed pretty well and managed to reach the plateau (plastic deformation).
After that I tried to do the exactly same simulation but using 2D shell elements (parabolic order), bi-linear material (LGDISP is on). In such case during the analysis a plateau (plastic deformation) wasn't reached. Solver managed only capture the elastic-plastic transition and then stopped because of calculations resulting in divergency.
For both analysis I used same parameters, material properties and force. For 2D calculation I also tried to increase number of increments.
Maybe someone could help me out to figure out or share some insights what I did wrong in analysis where I used shell elements?
P.S. these calculations are not meant to determine capacity of lifting lug but rather to learn how to perform a non-linear analysis and see the correlation regarding the hand calculations.
Shell setup:
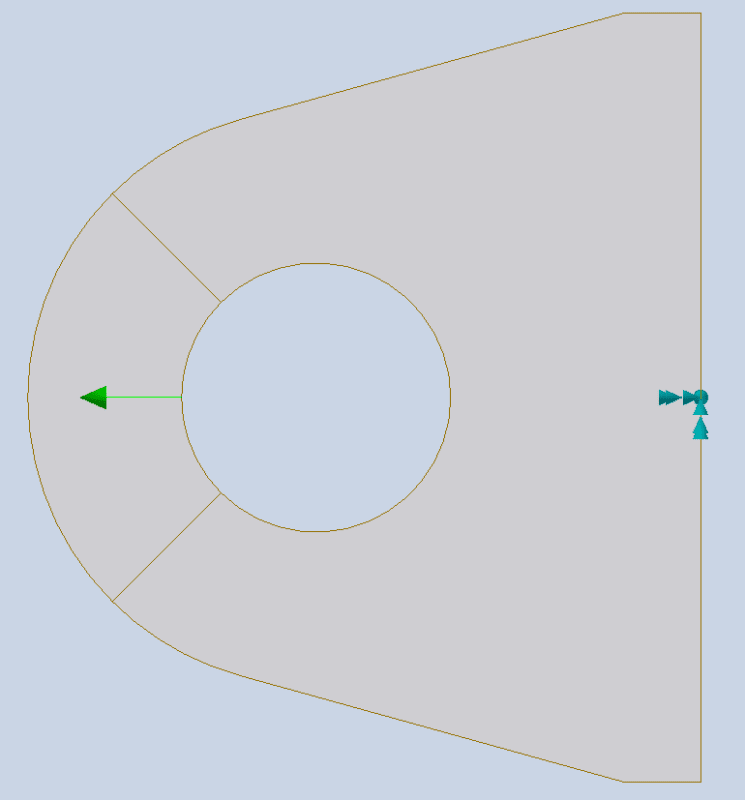
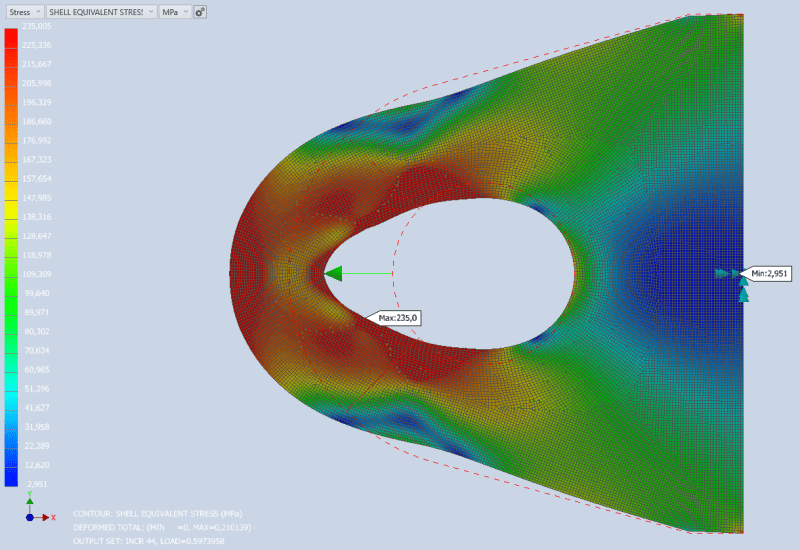
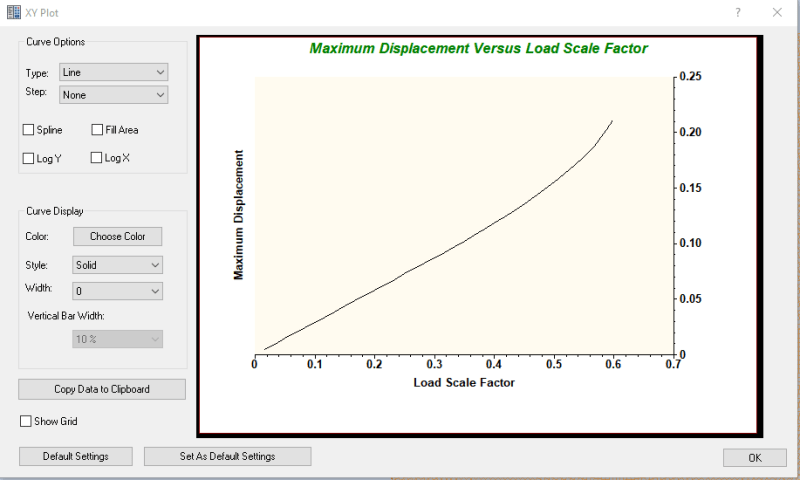
Solid setup:
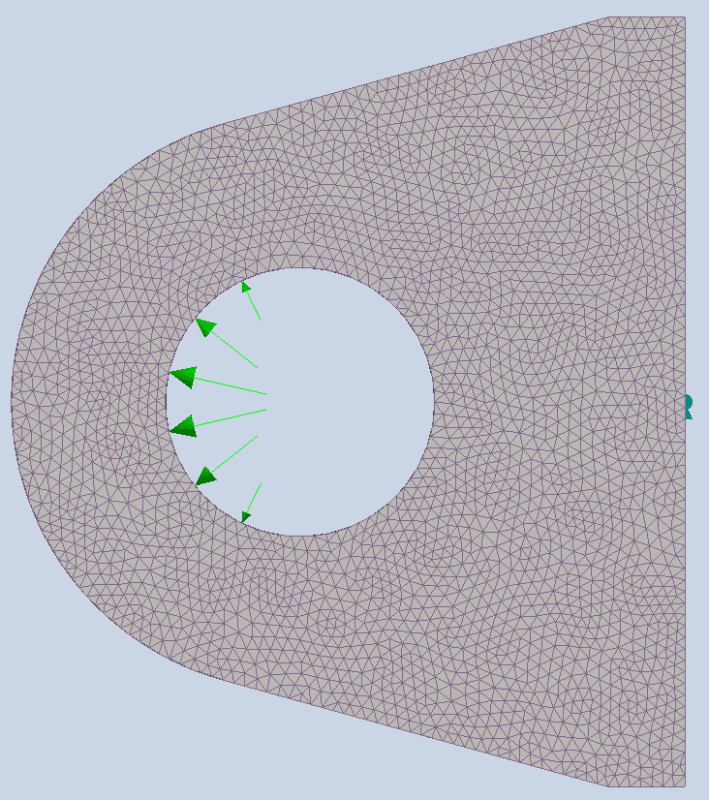
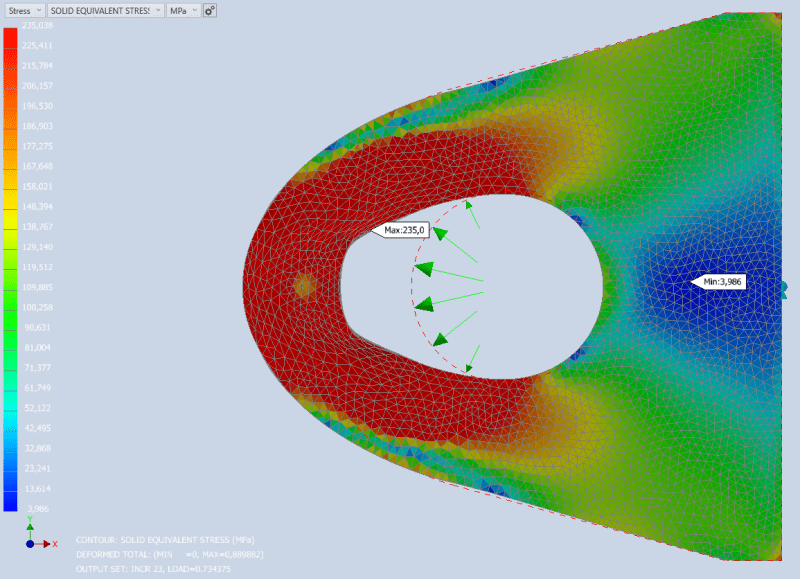
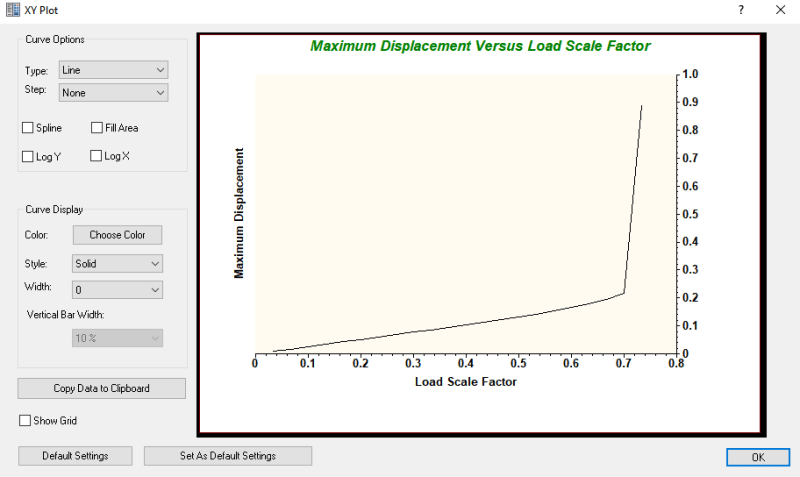