Iomcube
Chemical
- Dec 11, 2015
- 187
Cl2 & H2 should never mix ...but I have a situation where I have H2 compressor, H2 seal & Cl2 seal being fed by same water line.
What if x2 events happen simultaneously:
1] Supply water tank become empty so water line is empty
2] H2 seal is CS (carbon steel) & the immersed line can develop pitting holes & small H2 can be present in the top ullage of H2 seal
...in case 1st event is true this H2 will be sucked into Cl2 seal via empty water line (bcz Cl2 seal is under suction)
What if x2 events happen simultaneously:
1] Supply water tank become empty so water line is empty
2] H2 seal is CS (carbon steel) & the immersed line can develop pitting holes & small H2 can be present in the top ullage of H2 seal
...in case 1st event is true this H2 will be sucked into Cl2 seal via empty water line (bcz Cl2 seal is under suction)
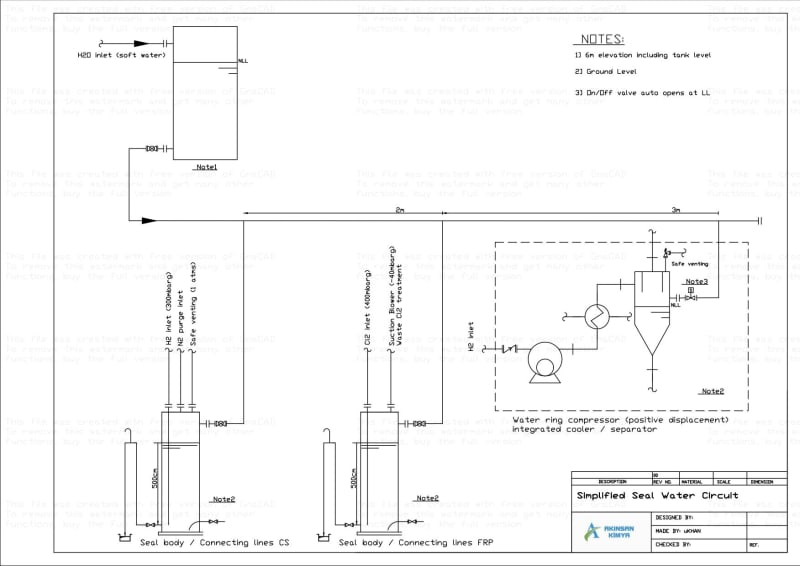