Hi fellow engineers
I’m experiencing an issue with the transition between two conveyor belts — from the belt coming out of the cooler to the next one.
Occasionally, the product comes out misaligned on the belt, possibly due to vibrations from the spiral tower cooler. The current guiding pins, as shown in the attached image, are not always sufficient to guide the product through. As I mentioned, the products sometimes exit at an angle, hit the tips of the pins, and cause a buildup on the belt, which leads to a line stop. I've also attached a video showing when this happens.
Is there a smarter or more flexible solution that can better handle products coming out at an wrong angle? I'm thinking perhaps an alternative to the pins — maybe some kind of rollers or wheels on the tips? I’m open to suggestions and ideas.
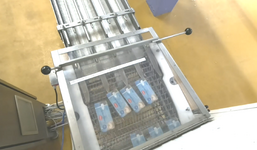
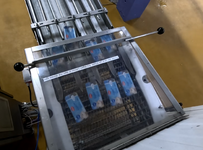
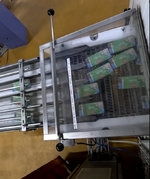
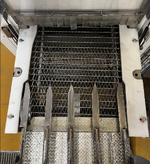
View attachment vlc-record-2025-04-15-14h37m31s-GX010199[1].MP4-.mp4
I’m experiencing an issue with the transition between two conveyor belts — from the belt coming out of the cooler to the next one.
Occasionally, the product comes out misaligned on the belt, possibly due to vibrations from the spiral tower cooler. The current guiding pins, as shown in the attached image, are not always sufficient to guide the product through. As I mentioned, the products sometimes exit at an angle, hit the tips of the pins, and cause a buildup on the belt, which leads to a line stop. I've also attached a video showing when this happens.
Is there a smarter or more flexible solution that can better handle products coming out at an wrong angle? I'm thinking perhaps an alternative to the pins — maybe some kind of rollers or wheels on the tips? I’m open to suggestions and ideas.
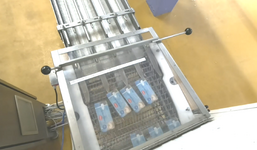
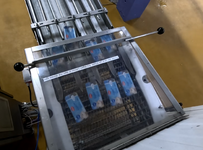
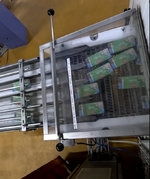
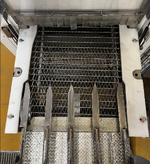
View attachment vlc-record-2025-04-15-14h37m31s-GX010199[1].MP4-.mp4