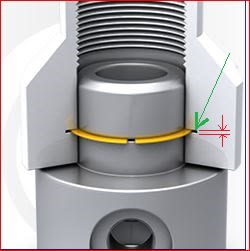
The location of the upper surface of the snap ring (green arrow)is less important than the width of the opening (red arrows).
A profile of surface within .020 back to a datum reference frame is added to green surface and a ± width of the slot within .005 is added for size.
The checker sent this drawing back to engineering as violating 8.2 profile per ASME Y14.5-2009.
"Where profile is used as a refinement of a size tolerance created by toleranced dimensions, the profile tolerance must be contained within the size limits".---meaning profile size (.020) must be smaller than width size (.005).
Profile .020|A|B|C|
width size .100 ± .0025 (per rule#1, green upper snap ring surface should be only flat within .005)
Is the checker correct? Why such a provision (8.2) in 2009 standard? If his interpretation is wrong what exactly is he missing?