TEDstruc
Civil/Environmental
- Dec 6, 2017
- 43
Does anyone have any experience calculating prying action on beam clamps, such as the below example? In this case assume the flange of the WT below is stiff enough to prevent prying. Could you provide some guidance on how to determine prying force to add to initial bolt tension? I'm assuming prying force will be applied at the round bar, but would appreciate any guidance for this somewhat unique situation. These clamps are commonly used in car plants.
The formula for the typical scenario with a WT or pair of angles bolted to a hanger don't seem to cover this scenario.
Thanks in advance.
The formula for the typical scenario with a WT or pair of angles bolted to a hanger don't seem to cover this scenario.
Thanks in advance.
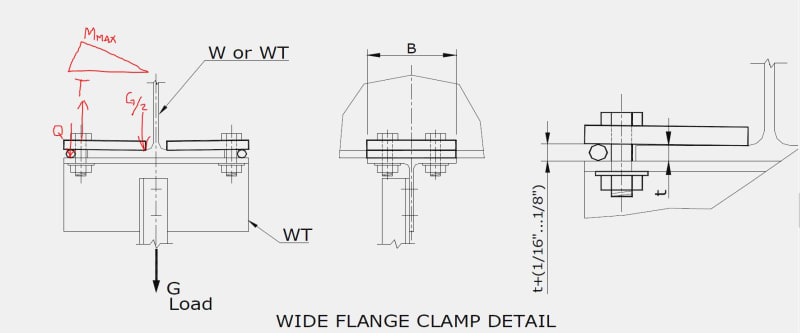