Hello, I could use a little help with a calculation that I've been struggling with.
I wish to mount a pulley to the end of a 20mm shaft whereby a M8 cap screw will secure it, there won't be a keyway or any other method of preventing the pulley from slipping, only the friction from the contact of the end faces as this will be a slip fit onto the shaft.
So this is where I need a little help, I want to calculate the torque required to make the joint fail so the pulley slips on the shaft. The pulley won't actually be under massive load but I'd like to be certain it's not going to fail.
Here's a few pictures of it.
Cheers, Tom
Sorry for large images.
I wish to mount a pulley to the end of a 20mm shaft whereby a M8 cap screw will secure it, there won't be a keyway or any other method of preventing the pulley from slipping, only the friction from the contact of the end faces as this will be a slip fit onto the shaft.
So this is where I need a little help, I want to calculate the torque required to make the joint fail so the pulley slips on the shaft. The pulley won't actually be under massive load but I'd like to be certain it's not going to fail.
Here's a few pictures of it.
Cheers, Tom
Sorry for large images.
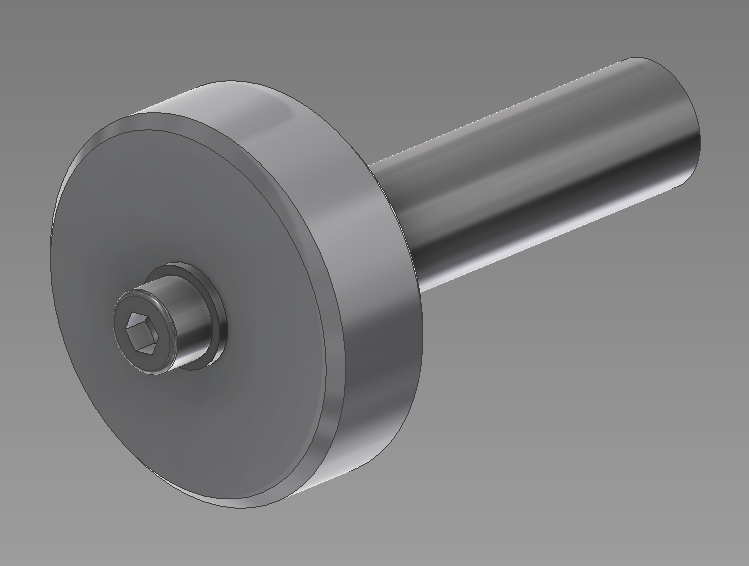
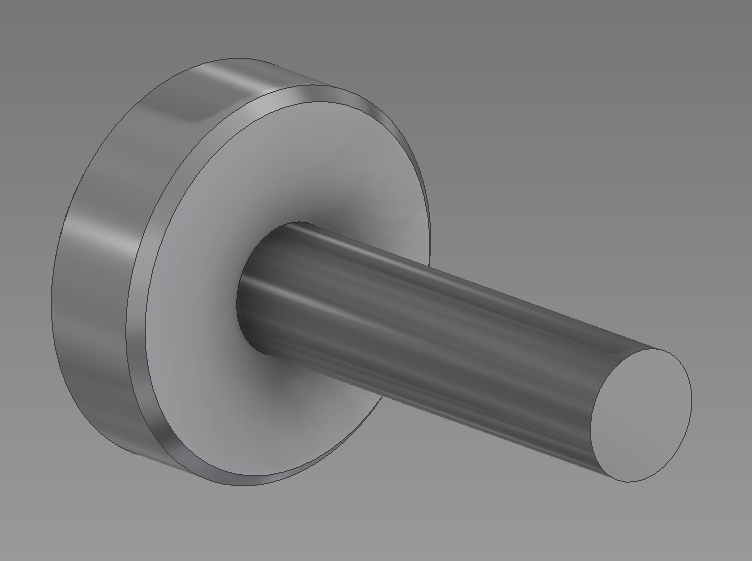
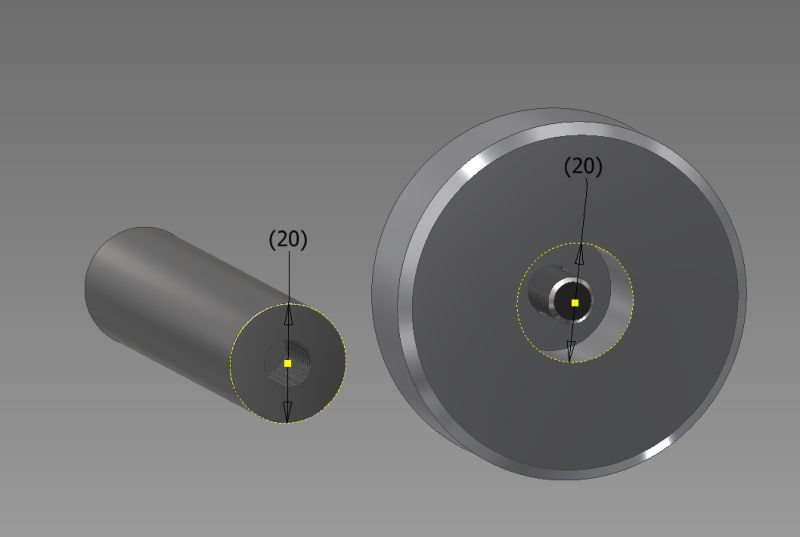
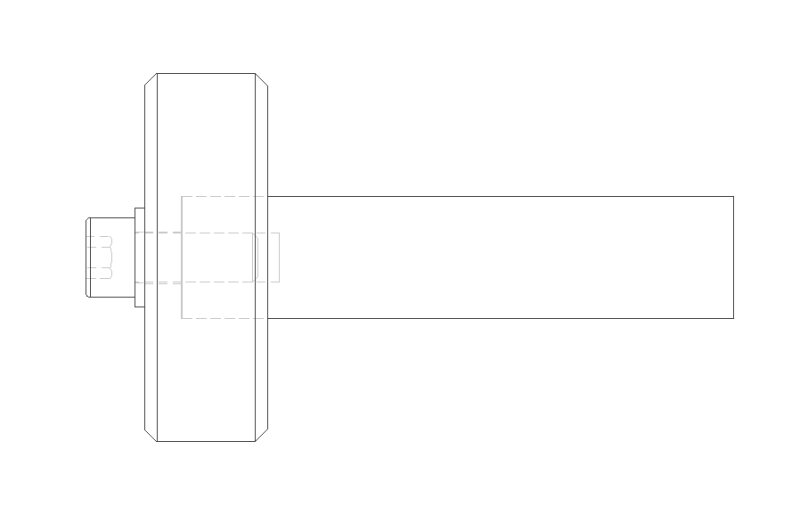