Austrian Lukas
Chemical
Hello,
I am a student and am doing my master thesis on membrane separation. The lab-scale membrane plant works with a CAT plunger pump (model 231) that enables flows of 8.7 lpm (2.3 gpm). The pressure I am working with is usually around 12 Bar (170 psi). The whole plant is designed to hold pressures up to 64 Bar, even though the pump can do up to 103 Bar (1500 psi). After the pump a pulsation damper is installed:
When I started my work several months ago everything was working fine. At one point however (after working at higher pressures between 50-60 Bar (800 psi) for a few hours), the pressure of the flow after the pump started pulsating +/- 2 Bar (30psi) and I could not find a solution for this problem. This pulsation was clearly visible on the analoge pressure gauge. The pulsation is smaller at lower pressures and increases at higher ones. At 30 Bar (430 psi) and higher the pulsation suddenly stops and the pressure becomes stable.
I tried cleaning the plant using NaOH and later H2SO4 as I suspected that maybe parts of the feed might have clogged some of the pipes. However, that did not help.
Due to the pulsation I can not continue with my experiments, as the pressure needs to be stable to obtain representative results. Also I am afraid that the problem gets even worse if I continue to use the plant like this.
Does someone have an idea what could be the problem here? I would be really thankful for any suggestions!
I am a student and am doing my master thesis on membrane separation. The lab-scale membrane plant works with a CAT plunger pump (model 231) that enables flows of 8.7 lpm (2.3 gpm). The pressure I am working with is usually around 12 Bar (170 psi). The whole plant is designed to hold pressures up to 64 Bar, even though the pump can do up to 103 Bar (1500 psi). After the pump a pulsation damper is installed:
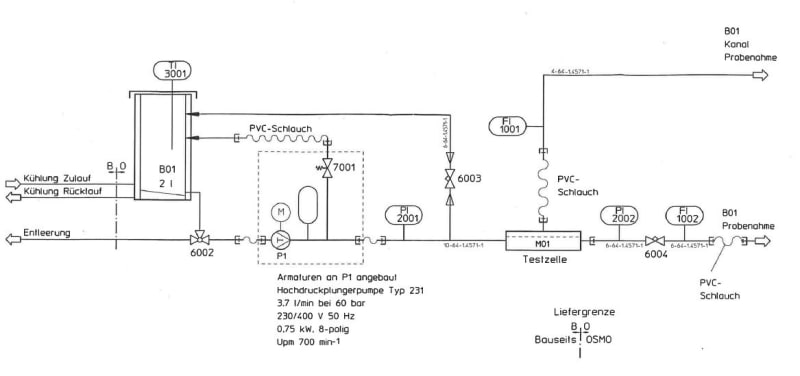
When I started my work several months ago everything was working fine. At one point however (after working at higher pressures between 50-60 Bar (800 psi) for a few hours), the pressure of the flow after the pump started pulsating +/- 2 Bar (30psi) and I could not find a solution for this problem. This pulsation was clearly visible on the analoge pressure gauge. The pulsation is smaller at lower pressures and increases at higher ones. At 30 Bar (430 psi) and higher the pulsation suddenly stops and the pressure becomes stable.
I tried cleaning the plant using NaOH and later H2SO4 as I suspected that maybe parts of the feed might have clogged some of the pipes. However, that did not help.
Due to the pulsation I can not continue with my experiments, as the pressure needs to be stable to obtain representative results. Also I am afraid that the problem gets even worse if I continue to use the plant like this.
Does someone have an idea what could be the problem here? I would be really thankful for any suggestions!