MechNerd08
Mechanical
Hello All,
I did a pump performance test on a recently overhauled horizontal split-case pump for a potable water system. Under normal operating conditions, pump was operating slightly off curve (tank elevation was high) but was within our internal acceptable range. We typically do a pump performance test before returning pump for service to get a baseline for future troubleshooting and to verify how successful pump overhaul was.
However, I noticed that at pump shut-off, pressure was significantly lower than I expected and once valve was fully opened and operating under normal conditions, pump had lost about 360 gpm while the suction/discharge pressures were the same as before testing started. Additionally, the pump sounded like it was cavitating or recirculating on the pump inboard side. Pump was shut off and verified no air was trapped in the pump and all valves were ensured to be working properly or fully opened. Pump was turned back on and was still underperforming. Pump is across the line and speed was verified to be similar to before.
I am thinking that during shut-off, something internally may have shifted and is causing pump to recirculate inside the casing. Vibration slightly increased but assumed it was due to noise coming from internal. Could there be anything else that could have caused a drop in performance like this? Any help/advice would be greatly appreciated. Below is data from test and a graph of test points compared to pump curve.
Pump Design Point - 2050 gpm at 410 ft
Operating Point
Suction Pressure - 21.1 psi
Discharge Pressure - 194.4 psi
Flow - 1885 gpm
Shut-Off
Suction Pressure - 21.1 psi
Discharge Pressure - 229.3 psi
Flow - 0 gpm
Post-Test
Suction Pressure - 21.1 psi
Discharge Pressure - 194.4 psi
Flow - 1526 gpm
I did a pump performance test on a recently overhauled horizontal split-case pump for a potable water system. Under normal operating conditions, pump was operating slightly off curve (tank elevation was high) but was within our internal acceptable range. We typically do a pump performance test before returning pump for service to get a baseline for future troubleshooting and to verify how successful pump overhaul was.
However, I noticed that at pump shut-off, pressure was significantly lower than I expected and once valve was fully opened and operating under normal conditions, pump had lost about 360 gpm while the suction/discharge pressures were the same as before testing started. Additionally, the pump sounded like it was cavitating or recirculating on the pump inboard side. Pump was shut off and verified no air was trapped in the pump and all valves were ensured to be working properly or fully opened. Pump was turned back on and was still underperforming. Pump is across the line and speed was verified to be similar to before.
I am thinking that during shut-off, something internally may have shifted and is causing pump to recirculate inside the casing. Vibration slightly increased but assumed it was due to noise coming from internal. Could there be anything else that could have caused a drop in performance like this? Any help/advice would be greatly appreciated. Below is data from test and a graph of test points compared to pump curve.
Pump Design Point - 2050 gpm at 410 ft
Operating Point
Suction Pressure - 21.1 psi
Discharge Pressure - 194.4 psi
Flow - 1885 gpm
Shut-Off
Suction Pressure - 21.1 psi
Discharge Pressure - 229.3 psi
Flow - 0 gpm
Post-Test
Suction Pressure - 21.1 psi
Discharge Pressure - 194.4 psi
Flow - 1526 gpm
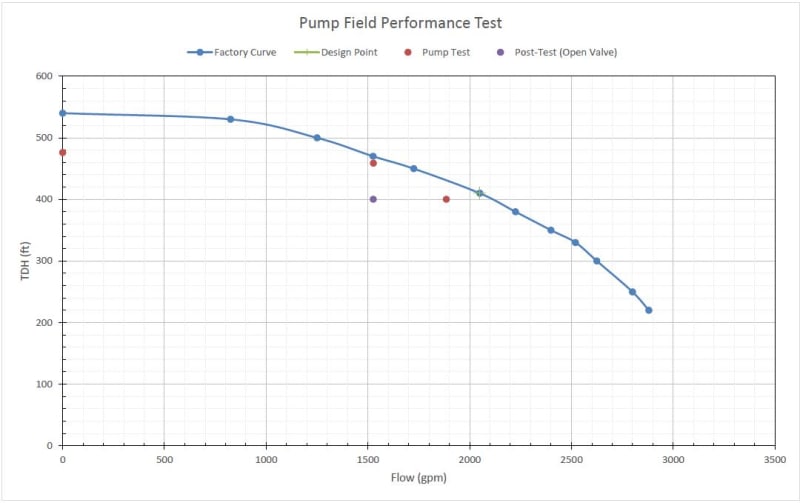