Pavan Kumar
Chemical
Hi All,
We have a Neutralization system in our plant that is used to Neutralize the acidic waste water with Mg(OH)2 used as Caustic. The waste water after Neutralization is sent to sewer when its meets the PH spec ( 5.5 < PH < 9.0). The Mg(OH)2 has a PH of 9, so the higher limit will increase. The Neutralization is done through a two tank system in which Caustic is added to first tank ( tank 1) and this water overflows to the second tank through dip pipes. The dip pipes have siphon breaker hole to prevent siphoning effect. The water from Tank 2 then over flows to the sewer tank which then drains to the sewer. Due to low residence time available for Mg(OH)2 to react, the Plant management has decided to install a recirculation pump that will recirculate the waste water between Tank 2 and Tank 1 ( and if needed back to the waste water tanks ) to increase the reaction time. Please see attached a rough hand sketch. The idea is to allow the Caustic to react completely to increase the PH above 5.5 at which point we can drain or over flow the water to sewer via sewer tank.
I am tasked with sizing and installation of the recirculation pump and piping. The pumped fluid( neutralized water) has a density of 66.64 lb/ft3 ( Sp.gr = 1.06) and a viscosity of 10 cP ( approximately, will be confirmed by measurement later next week). The fluid temperature is 70 Deg C The fluid is a thin slurry having 20% solids that will settle if left undisturbed for a couple of minutes. The fluid is considered to be Newtonian. The system has interlock to stop the acidic waste water pump in when the PH is less than 5.5. The waste water pump has a permissive to manually start the pump only when the PH is greater than 5.5. In the same way the Caustic pump stops when the PH is greater than 9.0. Also the permissive allows the Caustic pump to be manually started by operator when the PH is less than 9.0. The Neutralized water which meets the PH spec is then allowed to either over flow from Tank 2 or drain it from Tank 2.
My questions are as follows :
1. To perform the line pressure drop calculation and pump sizing calculations I can use the regular friction loss calculations (3K Method) with the above noted density and viscosity for a decided recirculation flow rate?.
2. For the pump selection:
(i)I will convert the vendor given pump curves ( for water ) to my fluid using the methodology given in ANSI/HI 9.6.7 - 2010 and calculate the power.
(ii) I will also the vendor to give me the curves based on my fluid and I will verify these vendor curves with my corrected curves.
(iii) I will also check the starting and operating Torque for my viscous fluid.
3. I will check with the vendor on the proper selection for a suitable mechanical sealing system.
4. I will maintain the line velocity above the terminal velocity to prevent the solids from settling.
I want to check if the above steps are sufficient and if missed anything?. Your comments and suggestions will be very helpful to me.
Thanks and Regards,
Pavan Kumar
We have a Neutralization system in our plant that is used to Neutralize the acidic waste water with Mg(OH)2 used as Caustic. The waste water after Neutralization is sent to sewer when its meets the PH spec ( 5.5 < PH < 9.0). The Mg(OH)2 has a PH of 9, so the higher limit will increase. The Neutralization is done through a two tank system in which Caustic is added to first tank ( tank 1) and this water overflows to the second tank through dip pipes. The dip pipes have siphon breaker hole to prevent siphoning effect. The water from Tank 2 then over flows to the sewer tank which then drains to the sewer. Due to low residence time available for Mg(OH)2 to react, the Plant management has decided to install a recirculation pump that will recirculate the waste water between Tank 2 and Tank 1 ( and if needed back to the waste water tanks ) to increase the reaction time. Please see attached a rough hand sketch. The idea is to allow the Caustic to react completely to increase the PH above 5.5 at which point we can drain or over flow the water to sewer via sewer tank.
I am tasked with sizing and installation of the recirculation pump and piping. The pumped fluid( neutralized water) has a density of 66.64 lb/ft3 ( Sp.gr = 1.06) and a viscosity of 10 cP ( approximately, will be confirmed by measurement later next week). The fluid temperature is 70 Deg C The fluid is a thin slurry having 20% solids that will settle if left undisturbed for a couple of minutes. The fluid is considered to be Newtonian. The system has interlock to stop the acidic waste water pump in when the PH is less than 5.5. The waste water pump has a permissive to manually start the pump only when the PH is greater than 5.5. In the same way the Caustic pump stops when the PH is greater than 9.0. Also the permissive allows the Caustic pump to be manually started by operator when the PH is less than 9.0. The Neutralized water which meets the PH spec is then allowed to either over flow from Tank 2 or drain it from Tank 2.
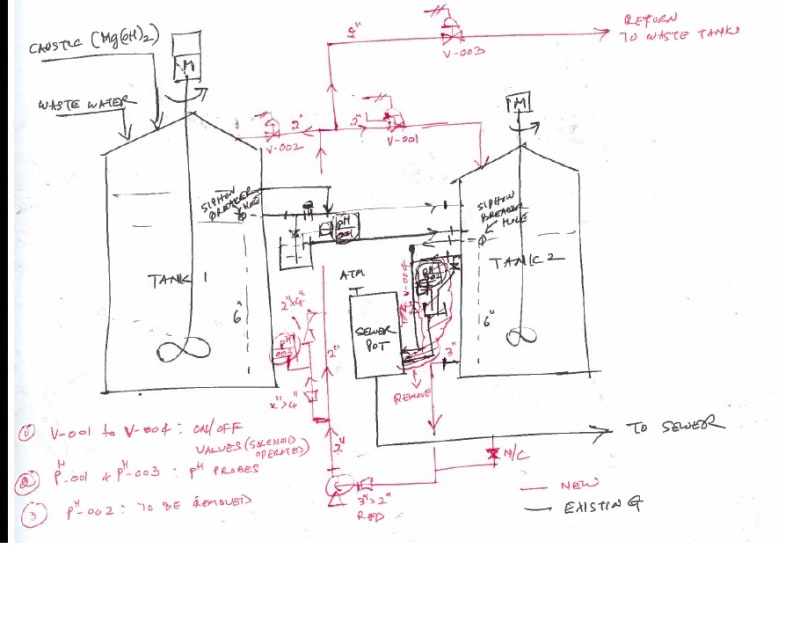
My questions are as follows :
1. To perform the line pressure drop calculation and pump sizing calculations I can use the regular friction loss calculations (3K Method) with the above noted density and viscosity for a decided recirculation flow rate?.
2. For the pump selection:
(i)I will convert the vendor given pump curves ( for water ) to my fluid using the methodology given in ANSI/HI 9.6.7 - 2010 and calculate the power.
(ii) I will also the vendor to give me the curves based on my fluid and I will verify these vendor curves with my corrected curves.
(iii) I will also check the starting and operating Torque for my viscous fluid.
3. I will check with the vendor on the proper selection for a suitable mechanical sealing system.
4. I will maintain the line velocity above the terminal velocity to prevent the solids from settling.
I want to check if the above steps are sufficient and if missed anything?. Your comments and suggestions will be very helpful to me.
Thanks and Regards,
Pavan Kumar