Pavan Kumar
Chemical
Hi All,
I am working on a Anaerobic Digestion Project. The process involves heating the contents of the Hydrolysis and Digester tanks to 37 Deg C using a external Heat exchanger( with Glycol on the shell side) with a re-circlation pump. To develop a calculation spreadsheet I want to start with simple case assuming the tank contents to be just water. I want to calculate the heat input to this Heat exchanger to heat the tank contents from 10 Deg C to 37 Deg C. Pasted below is quick sketch. I want to know how to proceed with this calculation. I know the water temperature is not constant but would like get a methodology to start the calculations. Once I understand the methodology I will use the actual fluid properties. Any guidance would be very helpful.
Thanks and Regards,
Pavan Kumar
I am working on a Anaerobic Digestion Project. The process involves heating the contents of the Hydrolysis and Digester tanks to 37 Deg C using a external Heat exchanger( with Glycol on the shell side) with a re-circlation pump. To develop a calculation spreadsheet I want to start with simple case assuming the tank contents to be just water. I want to calculate the heat input to this Heat exchanger to heat the tank contents from 10 Deg C to 37 Deg C. Pasted below is quick sketch. I want to know how to proceed with this calculation. I know the water temperature is not constant but would like get a methodology to start the calculations. Once I understand the methodology I will use the actual fluid properties. Any guidance would be very helpful.
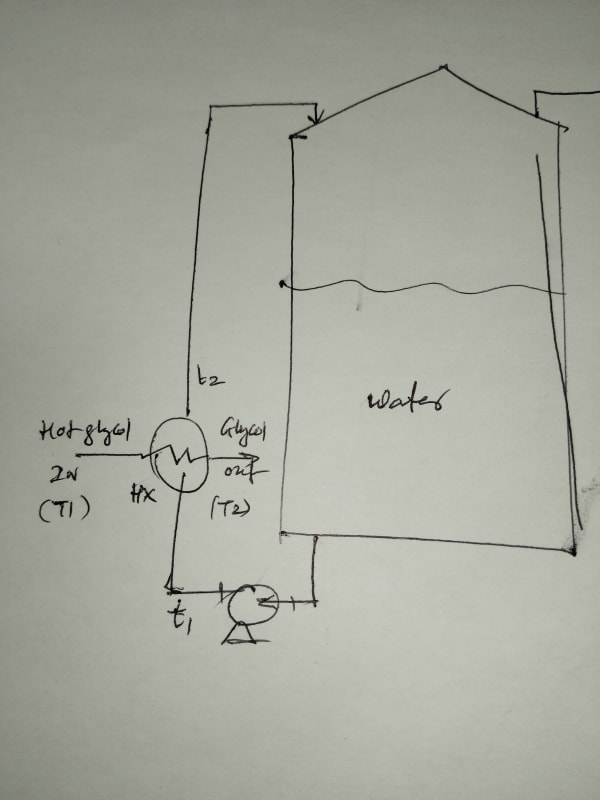
Thanks and Regards,
Pavan Kumar