Alfninux
Mechanical
- Apr 8, 2019
- 14
Hi everyone. I've a question related to the QUALITATIVE computation of the required torque to make a rotation.
The image shows a cross section. Two rigid bodies (hollow cylinder and elliptic base cylinder) and a deformable element are shown.
Supposing to know all the mechanical properties required, how do I compute (qualitatively) the torque required to make a 90deg rotation of the inner elliptic body in order to deforme the deformable element?
The deformable body and the outer cylinder are linked along their contact surface, and cannot slide
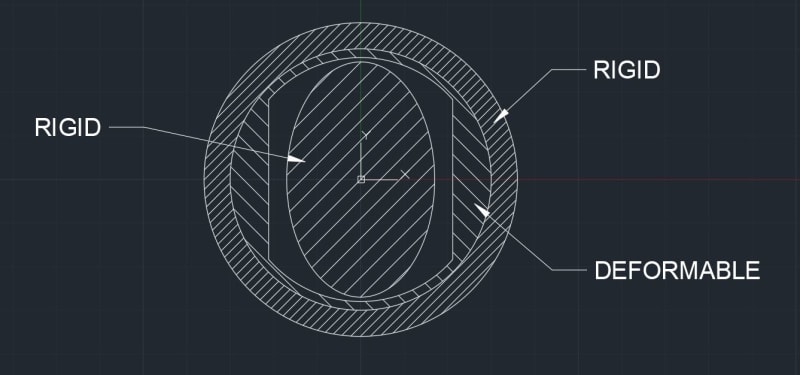
The image shows a cross section. Two rigid bodies (hollow cylinder and elliptic base cylinder) and a deformable element are shown.
Supposing to know all the mechanical properties required, how do I compute (qualitatively) the torque required to make a 90deg rotation of the inner elliptic body in order to deforme the deformable element?
The deformable body and the outer cylinder are linked along their contact surface, and cannot slide