Dear Abaqus users,
i am simulating crack propagation of a coating in conjunction with an indentor test. I was a bit surprised by the crack representation when i saw, that cracked elements would penetrate the slave body. You can see it in the picture i uploaded (the cracked elements penetrate the substrate (slave) which leads to a weird representation.
I am using a node to surface contact between the substrate and coating with a cohesive behaviour (damage and damage evolution). For cracks i use the XFEM with the cohesive zone model (crack initiation and evolution).
I would appreciate any tips.
i am simulating crack propagation of a coating in conjunction with an indentor test. I was a bit surprised by the crack representation when i saw, that cracked elements would penetrate the slave body. You can see it in the picture i uploaded (the cracked elements penetrate the substrate (slave) which leads to a weird representation.
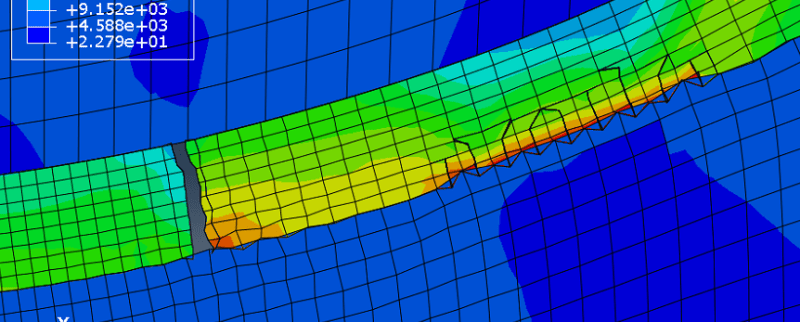
I am using a node to surface contact between the substrate and coating with a cohesive behaviour (damage and damage evolution). For cracks i use the XFEM with the cohesive zone model (crack initiation and evolution).
I would appreciate any tips.