Hi,
I would like to get opinions about pressure transmitter installation location in liquid service.
When measuring liquid pressure in pipeline, the pressure transmitter generally is installed below pipeline with a side pressure tap on pipeline.
This purpose is to vent freely entrapped gas/vapor(it can cause the measuring error) in liquid fluid through impulse line back to pipeline. Moreover, it can prevent the slurry or sediment in liquid fluid from entering impulse line(it can block the impulse line).
This is general practice as i know.
However, some owner or licensor recommend always installing a pressure transmitter above pipeline regardless the fluid status like vapor/gas, condensate, liquid, steam), and they tell it is for preventing measuring error caused by static head pressure.
I agree with that, but it is hard to understand easily.
So, i tried understanding with the fluid basis and Bernoulli's equation and the below is my conclusion.
<<Quoted>>
If the transmitter is installed at the below of pipeline with side pressure tap, the hydrostatic pressure generates due to an effect of elevation “h” which is impacted to gravity.
This makes the arbitrary datum plane “z” change from pipeline’s elevation(z) as the original reference level to transmitter’s elevation ground(h).
Vice versa, if the transmitter is installed above pipeline, the transmitter can measure only static pressure in pipeline since there is no impact of the hydrostatic pressure.
<<Unquoted>>
Is it right? please give your help for my understanding.
I would like to get opinions about pressure transmitter installation location in liquid service.
When measuring liquid pressure in pipeline, the pressure transmitter generally is installed below pipeline with a side pressure tap on pipeline.
This purpose is to vent freely entrapped gas/vapor(it can cause the measuring error) in liquid fluid through impulse line back to pipeline. Moreover, it can prevent the slurry or sediment in liquid fluid from entering impulse line(it can block the impulse line).
This is general practice as i know.
However, some owner or licensor recommend always installing a pressure transmitter above pipeline regardless the fluid status like vapor/gas, condensate, liquid, steam), and they tell it is for preventing measuring error caused by static head pressure.
I agree with that, but it is hard to understand easily.
So, i tried understanding with the fluid basis and Bernoulli's equation and the below is my conclusion.
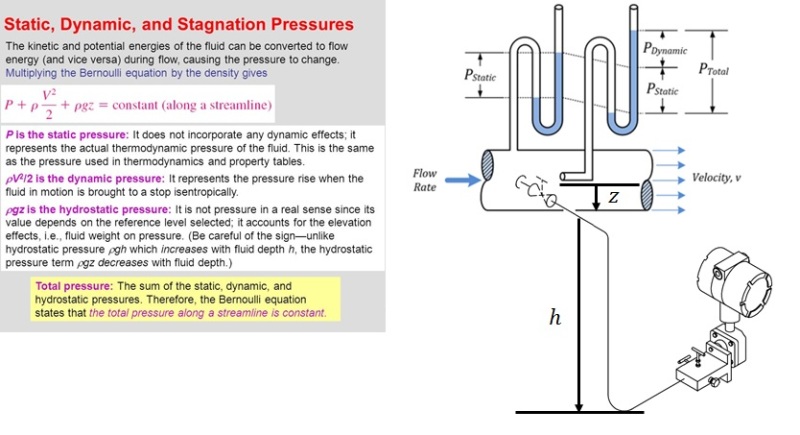
<<Quoted>>
If the transmitter is installed at the below of pipeline with side pressure tap, the hydrostatic pressure generates due to an effect of elevation “h” which is impacted to gravity.
This makes the arbitrary datum plane “z” change from pipeline’s elevation(z) as the original reference level to transmitter’s elevation ground(h).
Vice versa, if the transmitter is installed above pipeline, the transmitter can measure only static pressure in pipeline since there is no impact of the hydrostatic pressure.
<<Unquoted>>
Is it right? please give your help for my understanding.