David_HVAC_Learning
Mechanical
So, I've been reading this paper from Carrier in regards to the application of fans in commercial HVAC Equipment (Link to White Paper below) and I have a few questions regarding system effect. First, here is a following excerpt from the paper (Page 6), saying,
"Since the velocity profile at the outlet of a housed fan is not uniform, adequate straight duct distance must be allowed for the velocity profile to fully develop. (See Figure 7.) If a turn or bend in the duct takes place before this distance, the fan’s external static pressure (ESP) capability will diminish."
So, the thing I don't get is that, why is it so important for there not to be a bend coming out of a scroll housed centrifugal fan in comparison to bends and turns that happen all along a duct system? Why is it important that this one area (aside from the inlet) not have any bends or turns? I assume the velocity profile will be distorted in other bends in the ductwork, so why is it important for external static pressure for this one area? I don't know if there is a physics explanation to this or if it's just an observed phenomenon. Any input on this would be appreciated. Thank you. |
Link to Paper:
"Since the velocity profile at the outlet of a housed fan is not uniform, adequate straight duct distance must be allowed for the velocity profile to fully develop. (See Figure 7.) If a turn or bend in the duct takes place before this distance, the fan’s external static pressure (ESP) capability will diminish."
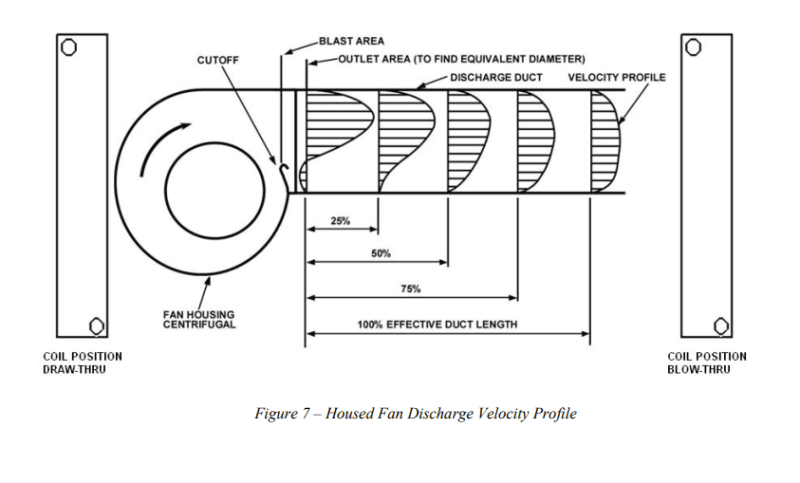
So, the thing I don't get is that, why is it so important for there not to be a bend coming out of a scroll housed centrifugal fan in comparison to bends and turns that happen all along a duct system? Why is it important that this one area (aside from the inlet) not have any bends or turns? I assume the velocity profile will be distorted in other bends in the ductwork, so why is it important for external static pressure for this one area? I don't know if there is a physics explanation to this or if it's just an observed phenomenon. Any input on this would be appreciated. Thank you. |
Link to Paper: