m.ahsaniftikhar
Mechanical
Hello all,
I am trying to design a telescopic elevating platform based on a rack and pinion configuration. The design is based on this video from youtube (click the link here). The video shows this in a horizontal configuration. I want to use this mechanism to build a vertical lift. For that, I need to perform some calculations. The telescoping effect achieved by this mechanism is of practical use in compact applications. Can anyone please help me out with the calculations needed to size the motors and the size if the rack and pinon for this? Please see the diagrams attached to get a better idea of the problem. I am particularly stuck with the effects of friction in this system.
I am trying to design a telescopic elevating platform based on a rack and pinion configuration. The design is based on this video from youtube (click the link here). The video shows this in a horizontal configuration. I want to use this mechanism to build a vertical lift. For that, I need to perform some calculations. The telescoping effect achieved by this mechanism is of practical use in compact applications. Can anyone please help me out with the calculations needed to size the motors and the size if the rack and pinon for this? Please see the diagrams attached to get a better idea of the problem. I am particularly stuck with the effects of friction in this system.
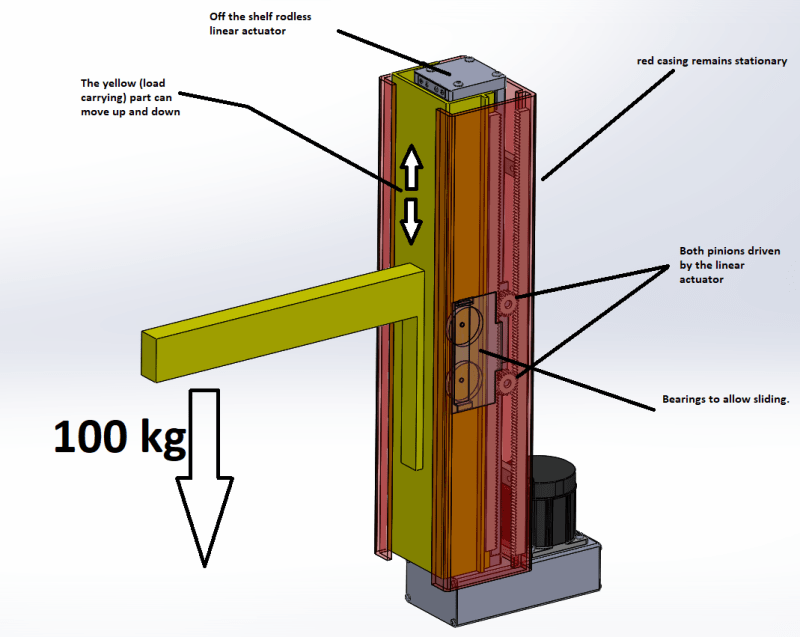