I have an engineering challenge.
I am in the process of designing a pick and place machine with a table moving in the X and Y direction.
For the Z-direction, a gripper is placed on a moving arm above the table.
For speed and cycle time purposes, the table is driven by a rack-and-pinion system. Such as:
The drives that are used are NEMA17 stepper motors without gearboxes for X and Y. The Z-drive has a gearbox on it.
However: If the system is powered-down, The table needs to be stabilized so that it cannot move around anymore. Also, the gripper-arm must be held in position when the power is switched off.
I have been trying to find an easy electrical system to lock this in place, but I have been unable to find anything useful up until now.
Requirements for actuator/brake-system:
Power source available: 5 volts and 12 volts.
System must be fail-safe. If the power is switched off, the brakes must be engaged.
Things that I came across, have tested, but did not work:
1) Solenoid actuator, 12V. Disadvantage: The max. pull-force is only available at the end of the stroke.
2) Magnet, electrical. Disadvantage: The max. pull-force is only available at the end of the stroke.
Do you happen to have any recommendations on this aspect?
Thanks in advance,
I am in the process of designing a pick and place machine with a table moving in the X and Y direction.
For the Z-direction, a gripper is placed on a moving arm above the table.
For speed and cycle time purposes, the table is driven by a rack-and-pinion system. Such as:
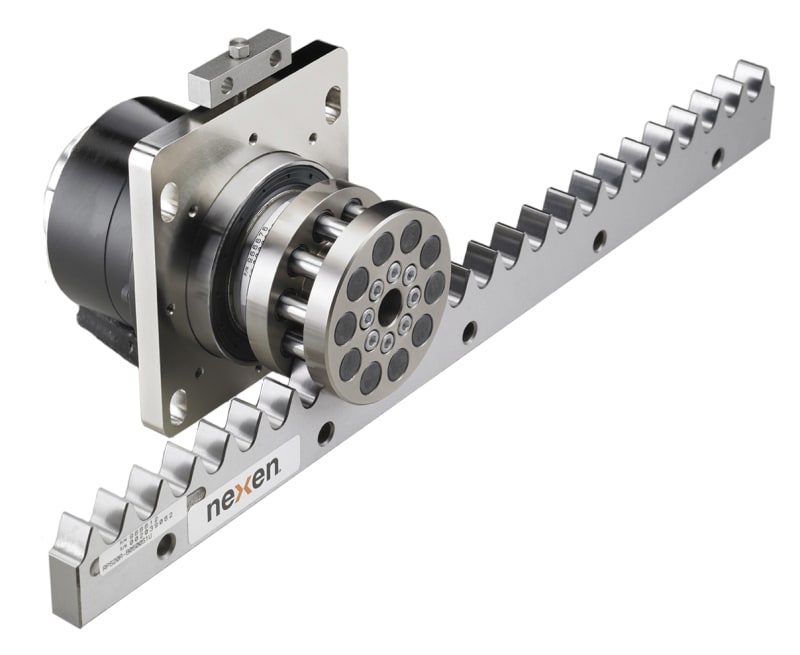
The drives that are used are NEMA17 stepper motors without gearboxes for X and Y. The Z-drive has a gearbox on it.
However: If the system is powered-down, The table needs to be stabilized so that it cannot move around anymore. Also, the gripper-arm must be held in position when the power is switched off.
I have been trying to find an easy electrical system to lock this in place, but I have been unable to find anything useful up until now.
Requirements for actuator/brake-system:
Power source available: 5 volts and 12 volts.
System must be fail-safe. If the power is switched off, the brakes must be engaged.
Things that I came across, have tested, but did not work:
1) Solenoid actuator, 12V. Disadvantage: The max. pull-force is only available at the end of the stroke.
2) Magnet, electrical. Disadvantage: The max. pull-force is only available at the end of the stroke.

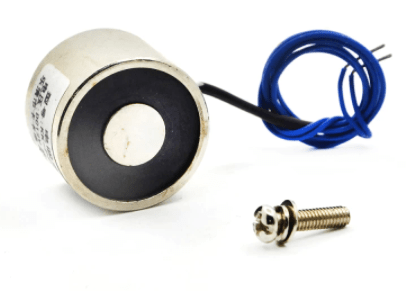
Do you happen to have any recommendations on this aspect?
Thanks in advance,