Mandrill22
Mechanical
I have a shaft with a radial load of 2300 N. I have two deep groove ball bearings on the shaft, pressed into rotating members. Is there an equation to calculate the amount of radial load the bearings absorb? I'm trying to figure out how much torque resistance there would be on the shaft's rotation. The shaft rotates with the long members. The drawing shown isn't fully representative of the system, but it gives you an idea.
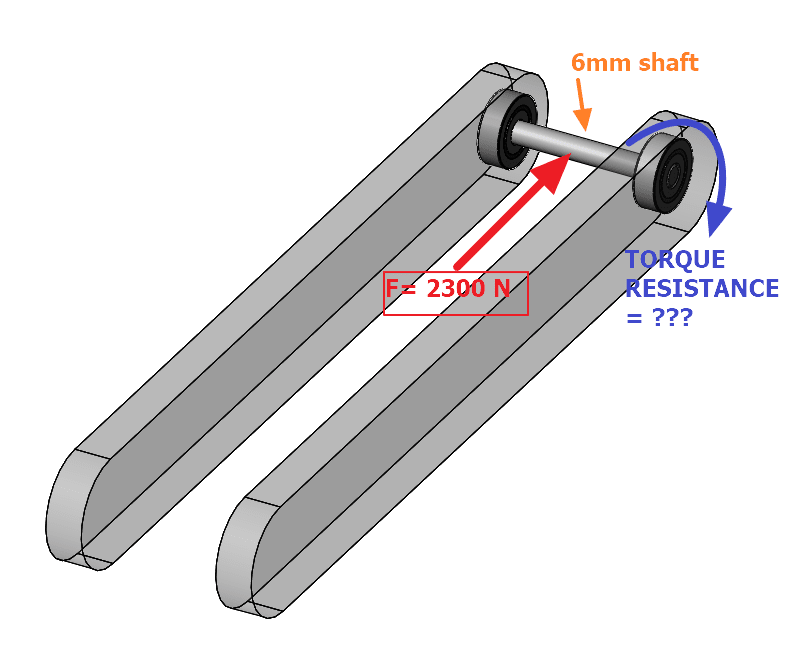