PARAMETERS
- Helping out with a field issue on someone else's design.
- Augured CIP piers for a pickleball screen wall fence thing. Seriously. Part solid, part chain link.
- Contractor allowed heavy rain to fall on the tops of the piers 60 min after casting.
- Ridiculously windy location. It's small scale but not as small as you might think.
- The owner is a municipality and they are traditionally quite concerned about durability.
- The posts supported on the CIP piers cannot be relocated without causing great pain.
- While I can think of several structurally acceptable solutions, I don't want to get too ridiculous with a damn pickleball fence. I'm a traditional tennis guy and generally annoyed by the pickleball striping on my local courts. Why can't the elderly just play Canasta like they used to?
QUESTION: What's to be done?
SOLUTIONS I'VE CONSIDERED
1) Current favorite. Chip the piers down to the bottom of the anchor bolts. Fill the hole back up with concrete and call it good. This probably does not rigorously deal with durability or anchorage but kind of feels "reasonable" to me.
2) Pull the piles out vertically somehow, augur bigger holes at the same location, and put the piles back. Expensive.
3) Install new piers located away from the posts and install a grade beam ring on the piers such that the superstructure posts can stay where they have to. Expensive. This does kind of feel like an excellent mechanical solution to me however.
4) Excavate the piles and come back with some kind of retaining structure:
a) Sonotube in engineered fill.
b) Sonotube on footing.
c) Retaining wall.
All crazy expensive.
- Helping out with a field issue on someone else's design.
- Augured CIP piers for a pickleball screen wall fence thing. Seriously. Part solid, part chain link.
- Contractor allowed heavy rain to fall on the tops of the piers 60 min after casting.
- Ridiculously windy location. It's small scale but not as small as you might think.
- The owner is a municipality and they are traditionally quite concerned about durability.
- The posts supported on the CIP piers cannot be relocated without causing great pain.
- While I can think of several structurally acceptable solutions, I don't want to get too ridiculous with a damn pickleball fence. I'm a traditional tennis guy and generally annoyed by the pickleball striping on my local courts. Why can't the elderly just play Canasta like they used to?
QUESTION: What's to be done?
SOLUTIONS I'VE CONSIDERED
1) Current favorite. Chip the piers down to the bottom of the anchor bolts. Fill the hole back up with concrete and call it good. This probably does not rigorously deal with durability or anchorage but kind of feels "reasonable" to me.
2) Pull the piles out vertically somehow, augur bigger holes at the same location, and put the piles back. Expensive.
3) Install new piers located away from the posts and install a grade beam ring on the piers such that the superstructure posts can stay where they have to. Expensive. This does kind of feel like an excellent mechanical solution to me however.
4) Excavate the piles and come back with some kind of retaining structure:
a) Sonotube in engineered fill.
b) Sonotube on footing.
c) Retaining wall.
All crazy expensive.
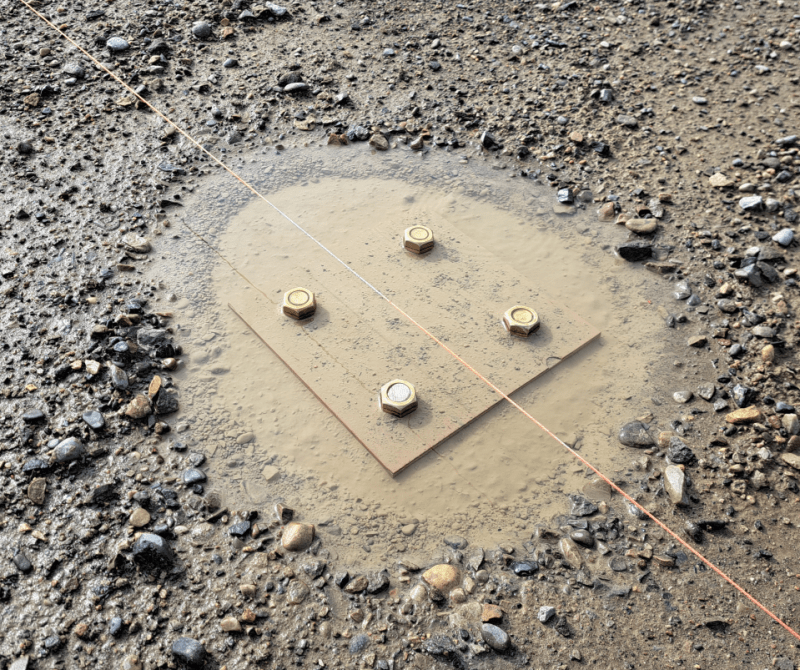
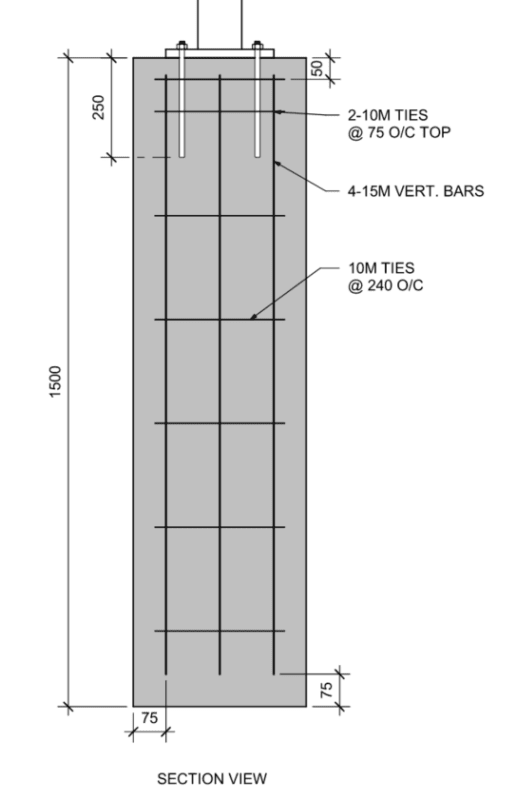
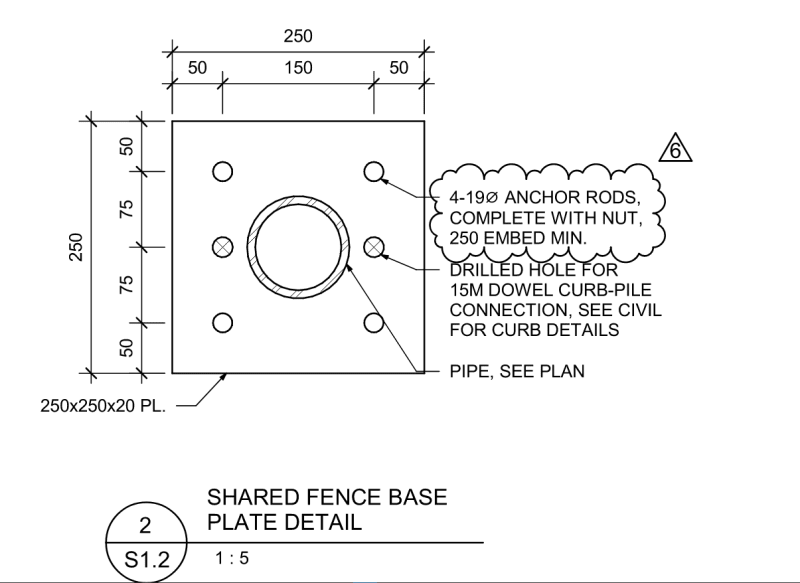