I see mechanical equipment being installed on top of raised concrete pads all the time. What is the reason those pads are raised? Why not make them same level as the rest of the slab? The one on the 2nd picture appears to be isolated from the floor slab, while the 1st one seems to be not.
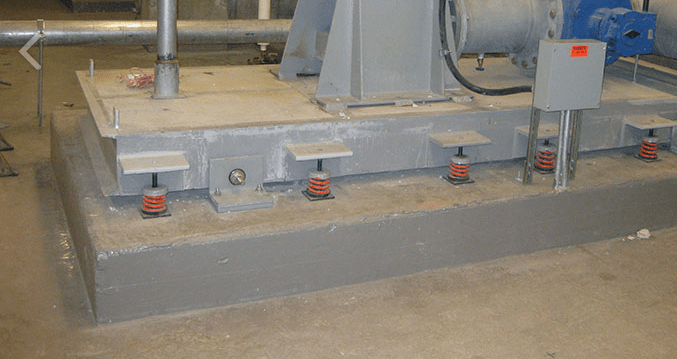
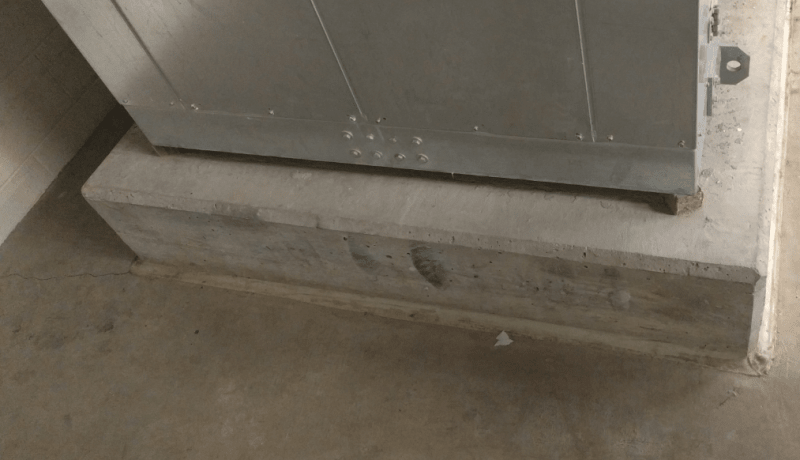