Hi All,
Just looking for some high-level comments or guidelines for modelling large(ish) cantilever in band beam floorplates (in RAM - RAPT is fine).
The floorplate is a 4m cantilever, 10.5m back span with a 9m tributary; a 400dp, 2.4m PT band beam with a 180thk PT slab structure has been adopted. Typical office loading of 1.5kPa SDL, 3kPa IL and 2.9kn/m for facade. Adopting the same concrete grades and PT profiles between RAPT and RAM results in the cantilever deflections that greatly differ:
RAPT: Circa 8-9mm
RAM: Circa 16-20mm
I am traditionally a RAPT user so I may be doing something wrong in with my RAM modelling.
Thanks in advance for any help (i'm sure that the "RAM vs RAPT" question has been asked loads of time)!
Just looking for some high-level comments or guidelines for modelling large(ish) cantilever in band beam floorplates (in RAM - RAPT is fine).
The floorplate is a 4m cantilever, 10.5m back span with a 9m tributary; a 400dp, 2.4m PT band beam with a 180thk PT slab structure has been adopted. Typical office loading of 1.5kPa SDL, 3kPa IL and 2.9kn/m for facade. Adopting the same concrete grades and PT profiles between RAPT and RAM results in the cantilever deflections that greatly differ:
RAPT: Circa 8-9mm
RAM: Circa 16-20mm
I am traditionally a RAPT user so I may be doing something wrong in with my RAM modelling.
Thanks in advance for any help (i'm sure that the "RAM vs RAPT" question has been asked loads of time)!
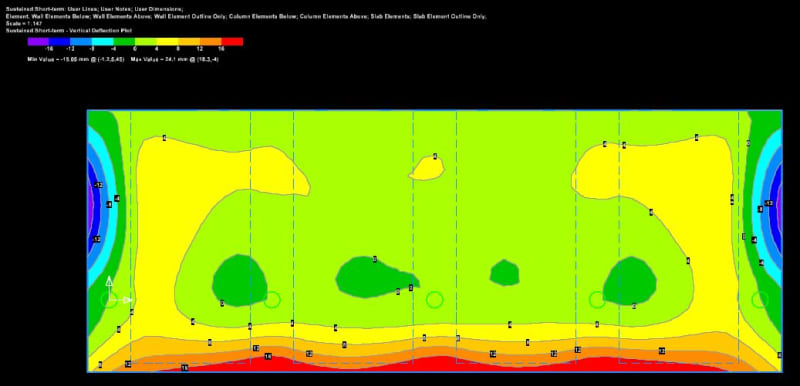
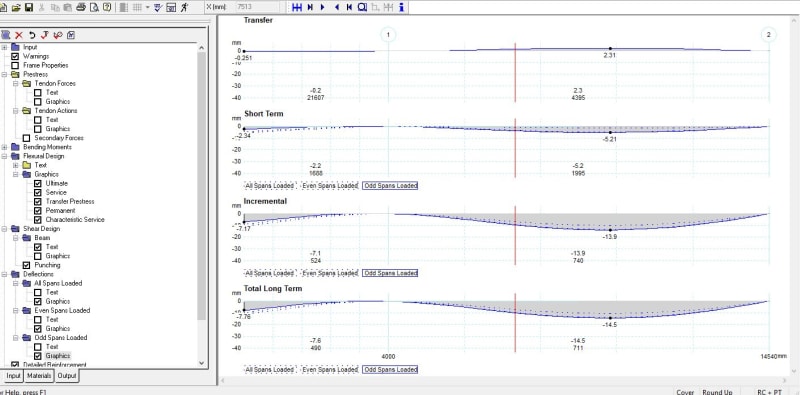