Hi everybody, I hope someone could help me solve a problem I'm having in anlyzing a component.
The component is basically a short mast, with circular section, crimpled to a support, at the other end there are some instruments.
I am performing random analysis through MSC.Random. Then eveluating the PSD response and the stress using the built-in tool of MSC.Random.
I'm having very strange results though: basically in every test I have performed (many test, with different constraints and different meshing) I realized that the elements where I attach the input acceleration are the most stressed. The problem increases when the mesh becomes smaller and more detailed.
Looking at the acceleration plot response I realized that there is a strong damping effect in the first element, as it absorb a big quantity of energy.
The stresses at the input nodes are incredibly high and unrealistic. (I'm talking of X*10^3 Mpa!! on a component that weight less than 200 grams and it not bigger than 250mm with moderate PSD loading)
Another strange effect is that plotting the CRMS of the Stress It apperars evident how the biggest part of the stresses is accumulated on the lowest frequency (10-80 Hz), while the hightest PSD inputs are between 50-300 Hz and the first frequency is around 160 Hz.
Basically seems some sorf of effect that tends to concentrate the deformation and so the stresses on the input nodes, but I cannot realy explain why.
I'm attaching some pictures:
Stresses:
Details:
CRMS Stress Plot:
Another example of a different meshes with even higher results, it seems that the smaller the mesh become the worst are the results!
I thank everybody who will be able to help me!
Ned
The component is basically a short mast, with circular section, crimpled to a support, at the other end there are some instruments.
I am performing random analysis through MSC.Random. Then eveluating the PSD response and the stress using the built-in tool of MSC.Random.
I'm having very strange results though: basically in every test I have performed (many test, with different constraints and different meshing) I realized that the elements where I attach the input acceleration are the most stressed. The problem increases when the mesh becomes smaller and more detailed.
Looking at the acceleration plot response I realized that there is a strong damping effect in the first element, as it absorb a big quantity of energy.
The stresses at the input nodes are incredibly high and unrealistic. (I'm talking of X*10^3 Mpa!! on a component that weight less than 200 grams and it not bigger than 250mm with moderate PSD loading)
Another strange effect is that plotting the CRMS of the Stress It apperars evident how the biggest part of the stresses is accumulated on the lowest frequency (10-80 Hz), while the hightest PSD inputs are between 50-300 Hz and the first frequency is around 160 Hz.
Basically seems some sorf of effect that tends to concentrate the deformation and so the stresses on the input nodes, but I cannot realy explain why.
I'm attaching some pictures:
Stresses:
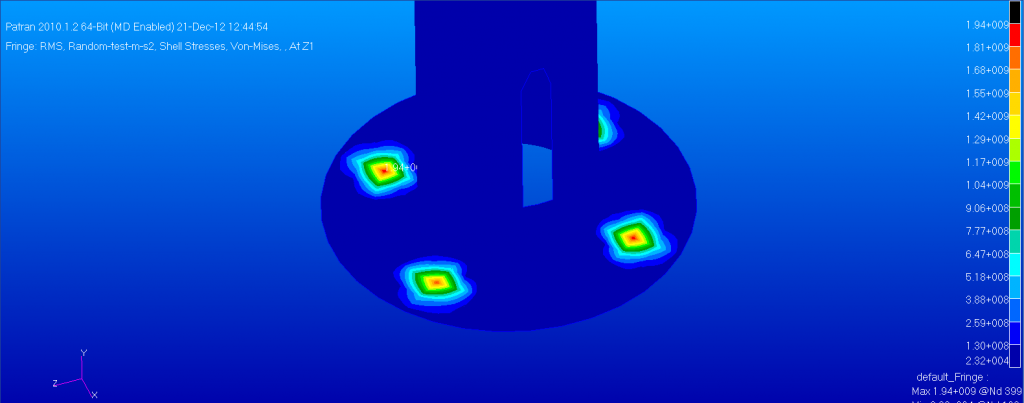
Details:
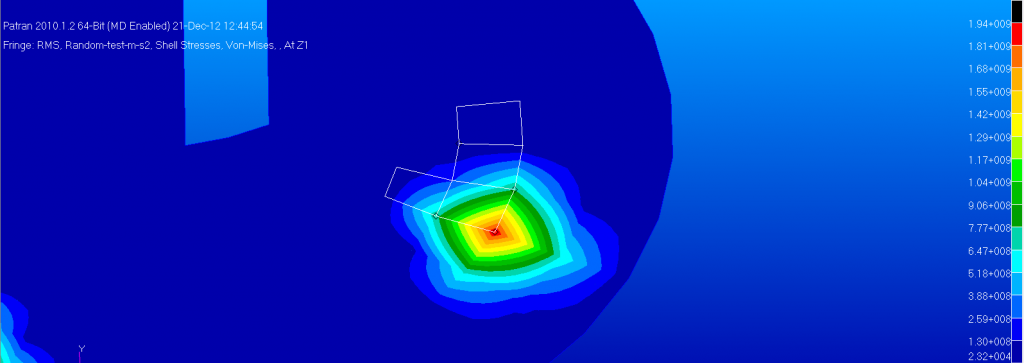
CRMS Stress Plot:
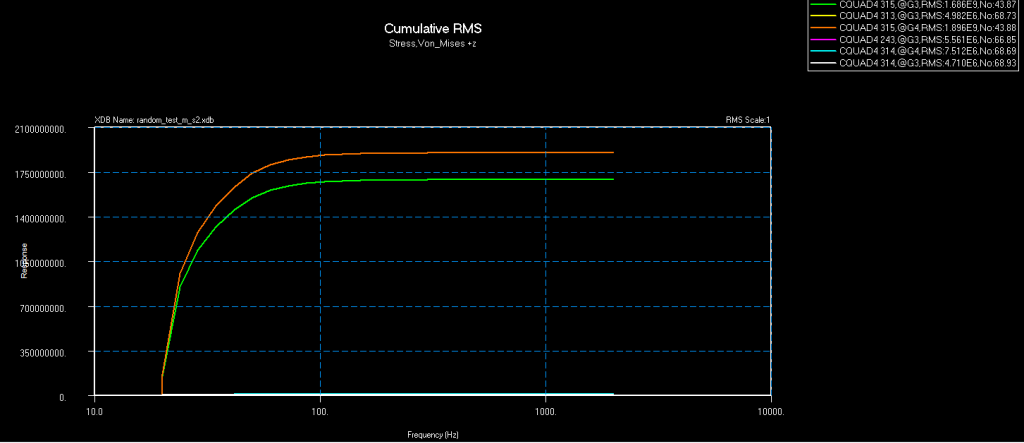
Another example of a different meshes with even higher results, it seems that the smaller the mesh become the worst are the results!
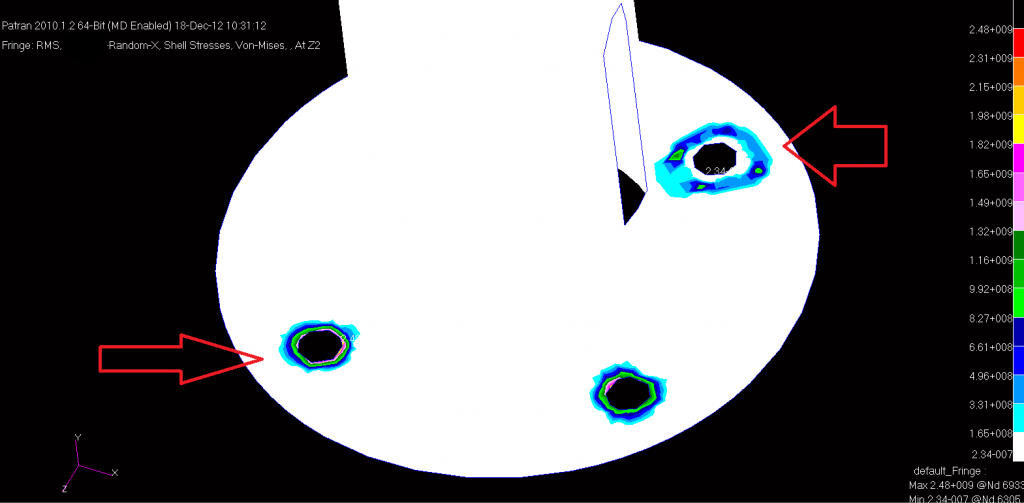
I thank everybody who will be able to help me!
Ned