We own 4 of these motors described below. The motors are tripping due to high vibration. Last week we found that the ratchet (NIDEC's design) is coming apart. This ratchet design uses pins to lock the shaft in place to prevent it from backspin.
1. Has anyone experienced this failure mode before where pins are pushed out of their boreholes (Image with red arrows and some notes)?
2. Also, if you take a closer look at the unedited image, there is a considerable amount of shavings in the pockets that are supposed to hold the ratchet pins when reversing. The pins will slide in the forward direction until they are held above the resting plate (the one with the pockets) until it coasts down and the pins slide down to engage. The wear damage is from only 9 months of intermittent operation (2 times per day, approx. 6 hours of operation). Has anyone experienced this level of wear?
3. The bottom plate is cast, shouldn't it be from the same material as pins or stronger?
Features:
Horsepower .............. 02500.00~00000.00 ~ KW: 1865
Enclosure ............... WPII
Poles ................... 08~00 ~ RPM: 900~0
Frame Size .............. 9606~PY
Phase/Frequency/Voltage.. 3~060~4160
Winding Type ............ Form Wound
Service Factor .......... 1.15
Insulation Class ........ Class "F" ~ Everseal
Altitude In Feet (Max) .. 3300 Ft.(1000 M)
Ambient In Degree C (Max) +40 C
Efficiency Class ........ Premium Efficiency
Application ............. Vertical Centrifugal Pump
Inverter Duty NEMA MG1 Part 31
Customer Part Number ....
Base Diameter (BD) 50
Flange Mounting on PE (AK) 36
AJ 45.00
BF 1.125
Special "BA" Dimension
Special "H" Dimension
Base Diameter (Inches) ....... 50
Non-Reverse Ratchet
Pricebook Thrust Value (lbs).. 16500
Customer Down Thrust (lbs) ... 46425
Customer Shutoff Thrust (lbs). 73124
Up Thrust (lbs) .............. 4950
Momentary Up Thrust
Inverter Duty Rating Details:
Load Type (Base Hz & Below) .. Variable Torque
Speed Range (Base Hz & Below). 4:1
VFD Service Factor 1.00
"AK" Dimension (Inches).. 36
Shaft Dimensions:~U=5.500 ~ AH/V=11.500
KEYWAY=1.250 ~ ES=9.000
Temperature Rise (Sine Wave): "B" Rise @ 1.0 SF (Resist)
Starting Method ......... Direct-On-Line Start
Duty Cycle .............. Continuous Duty
Sound Pressure Required (dBA) 85 dBa @ 1M Sound Pressure
Load Inertia: 606 ~ Standard Inertia: 41898 LB-FT2
200 % BDT ~ 60 % LRT
Number Of Starts Per Hour: NEMA
Motor Type Code ............ RVEI4
Rotor Inertia (LB-FT²) 3580 LB-FT²
Qty. of Bearings PE (Shaft) 1
Qty. of Bearings SE (OPP) 1
1. Has anyone experienced this failure mode before where pins are pushed out of their boreholes (Image with red arrows and some notes)?
2. Also, if you take a closer look at the unedited image, there is a considerable amount of shavings in the pockets that are supposed to hold the ratchet pins when reversing. The pins will slide in the forward direction until they are held above the resting plate (the one with the pockets) until it coasts down and the pins slide down to engage. The wear damage is from only 9 months of intermittent operation (2 times per day, approx. 6 hours of operation). Has anyone experienced this level of wear?
3. The bottom plate is cast, shouldn't it be from the same material as pins or stronger?
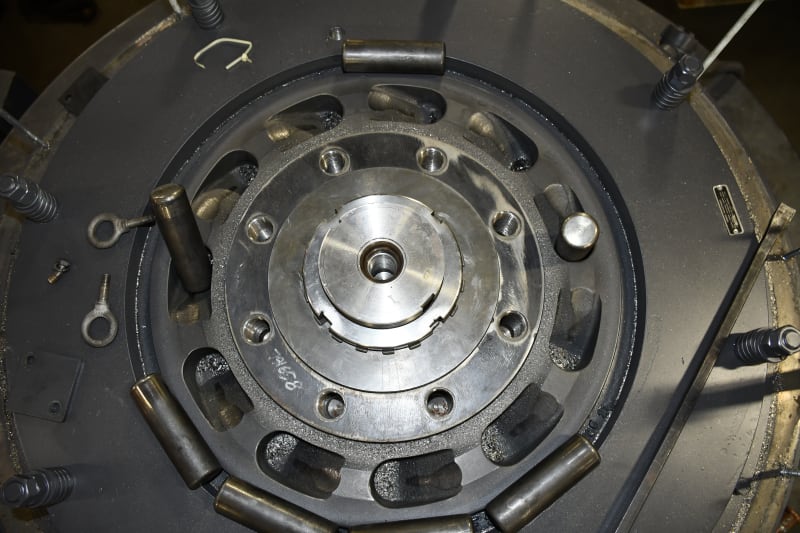
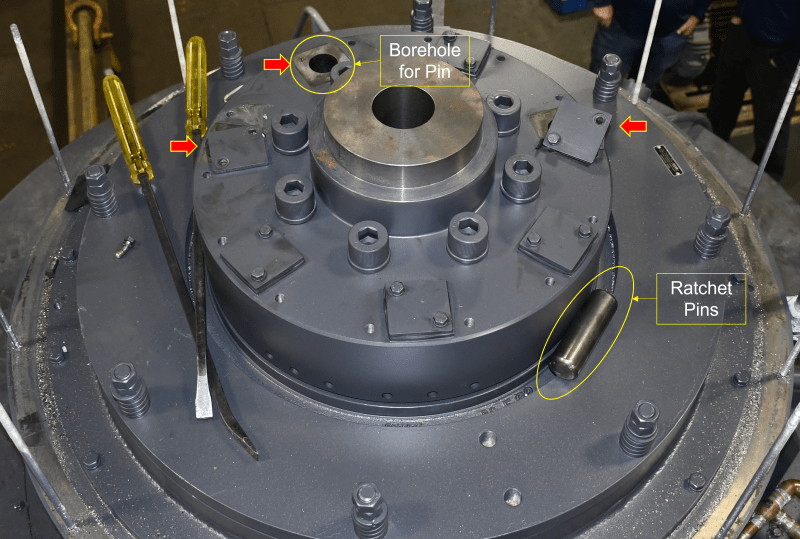
Features:
Horsepower .............. 02500.00~00000.00 ~ KW: 1865
Enclosure ............... WPII
Poles ................... 08~00 ~ RPM: 900~0
Frame Size .............. 9606~PY
Phase/Frequency/Voltage.. 3~060~4160
Winding Type ............ Form Wound
Service Factor .......... 1.15
Insulation Class ........ Class "F" ~ Everseal
Altitude In Feet (Max) .. 3300 Ft.(1000 M)
Ambient In Degree C (Max) +40 C
Efficiency Class ........ Premium Efficiency
Application ............. Vertical Centrifugal Pump
Inverter Duty NEMA MG1 Part 31
Customer Part Number ....
Base Diameter (BD) 50
Flange Mounting on PE (AK) 36
AJ 45.00
BF 1.125
Special "BA" Dimension
Special "H" Dimension
Base Diameter (Inches) ....... 50
Non-Reverse Ratchet
Pricebook Thrust Value (lbs).. 16500
Customer Down Thrust (lbs) ... 46425
Customer Shutoff Thrust (lbs). 73124
Up Thrust (lbs) .............. 4950
Momentary Up Thrust
Inverter Duty Rating Details:
Load Type (Base Hz & Below) .. Variable Torque
Speed Range (Base Hz & Below). 4:1
VFD Service Factor 1.00
"AK" Dimension (Inches).. 36
Shaft Dimensions:~U=5.500 ~ AH/V=11.500
KEYWAY=1.250 ~ ES=9.000
Temperature Rise (Sine Wave): "B" Rise @ 1.0 SF (Resist)
Starting Method ......... Direct-On-Line Start
Duty Cycle .............. Continuous Duty
Sound Pressure Required (dBA) 85 dBa @ 1M Sound Pressure
Load Inertia: 606 ~ Standard Inertia: 41898 LB-FT2
200 % BDT ~ 60 % LRT
Number Of Starts Per Hour: NEMA
Motor Type Code ............ RVEI4
Rotor Inertia (LB-FT²) 3580 LB-FT²
Qty. of Bearings PE (Shaft) 1
Qty. of Bearings SE (OPP) 1