Muhammad Mazher
Mechanical
- May 21, 2024
- 8
Hi everyone! I am seeking advice from experts regarding the root cause analysis for an incident at our petrochemical plant. Specifically, one of the critical blower fan's bearings on the coupling side seized, despite satisfactory oil level and condition. While one bearing remained operational, the incident has raised concerns about our maintenance practices. I am keen to understand potential issues with oil distribution and the effectiveness of lubrication within the bearing housing. Any insights or recommendations from experienced professionals would be greatly appreciated. I am attaching pictures for clear observation.
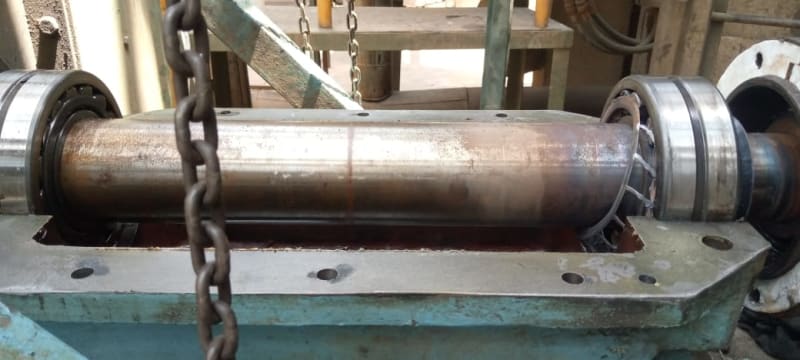
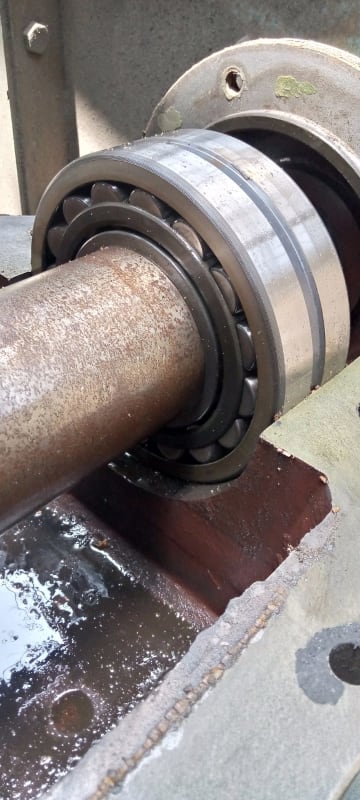
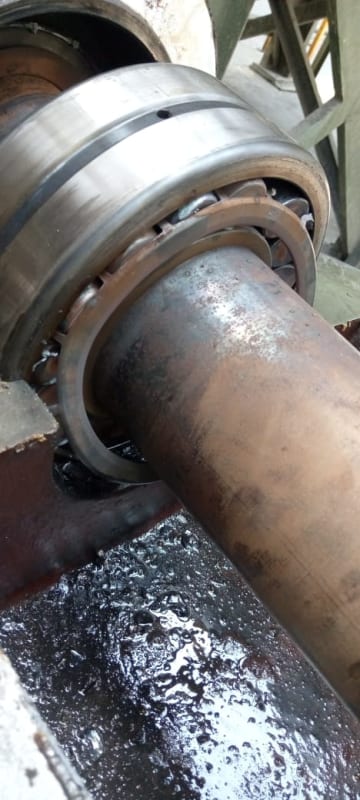
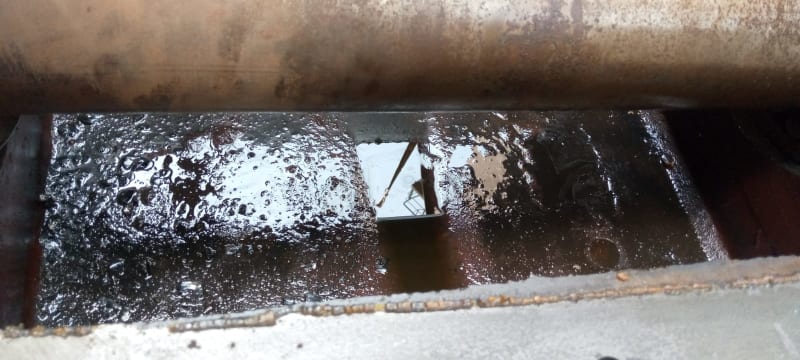
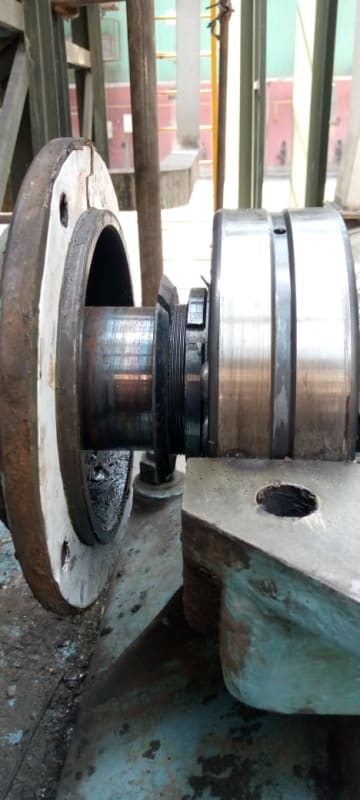
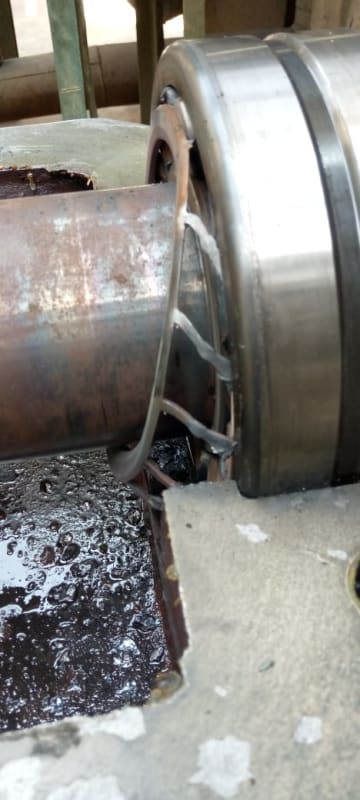
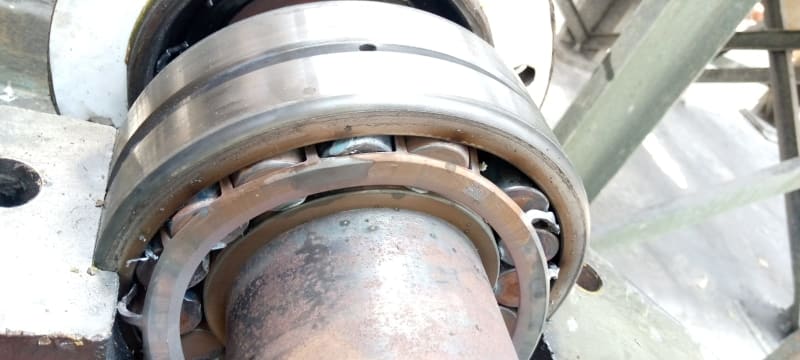
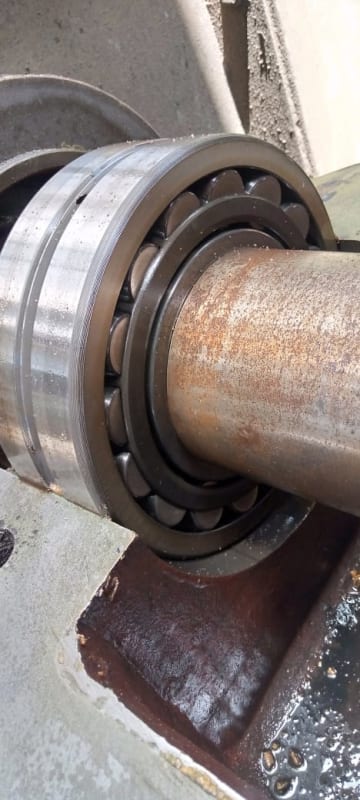
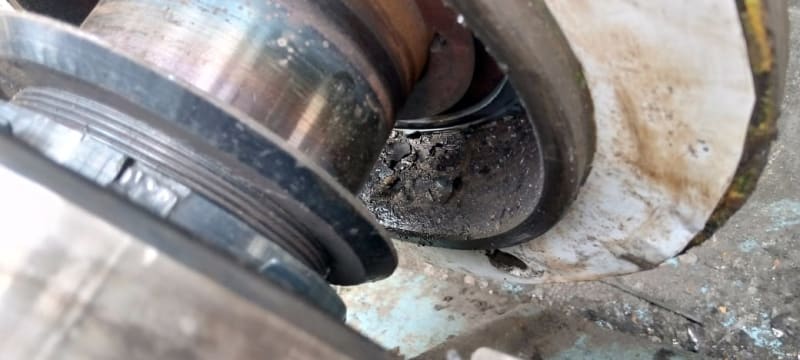
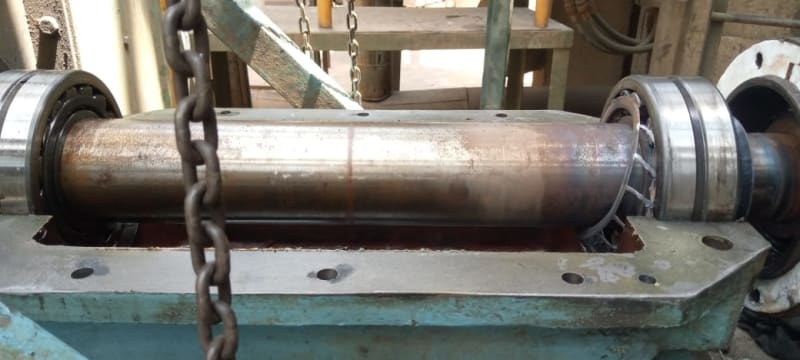
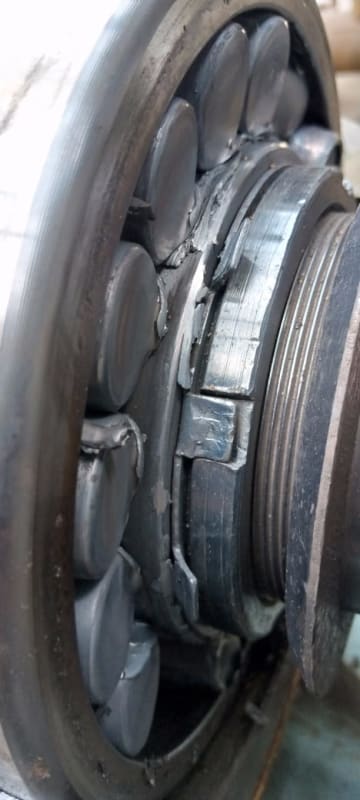
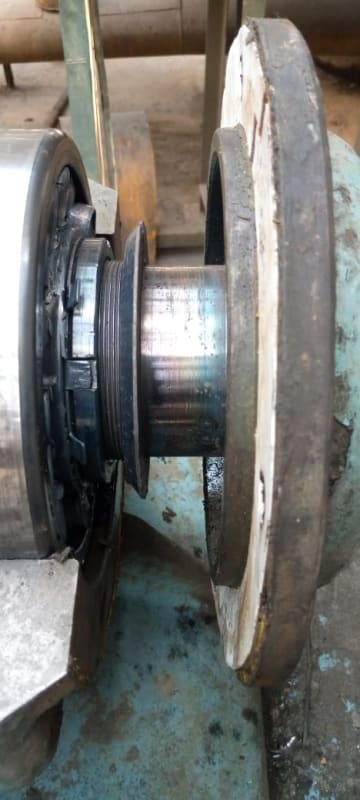
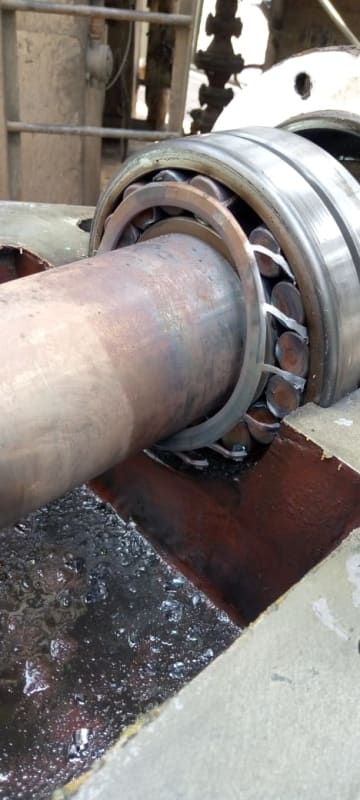
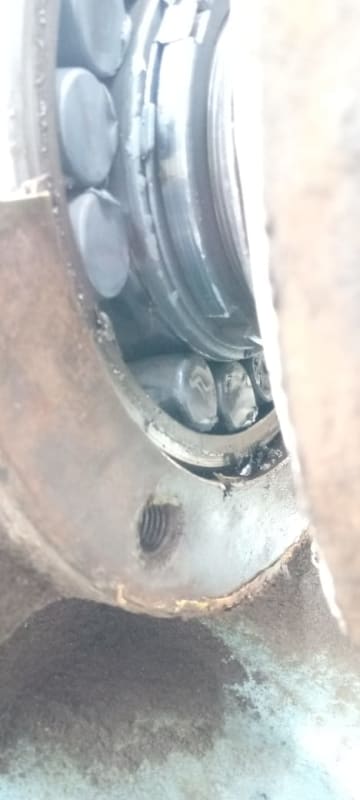
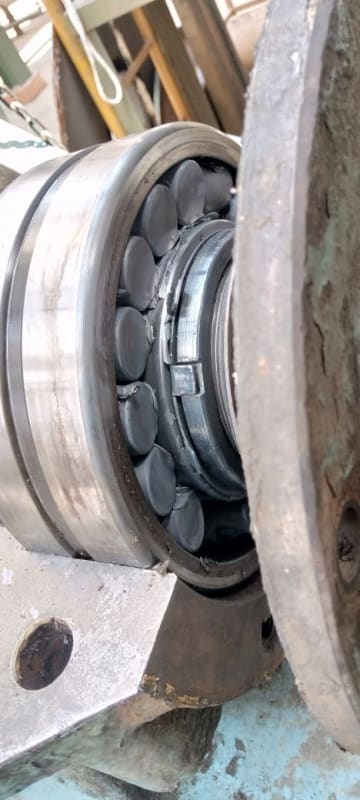
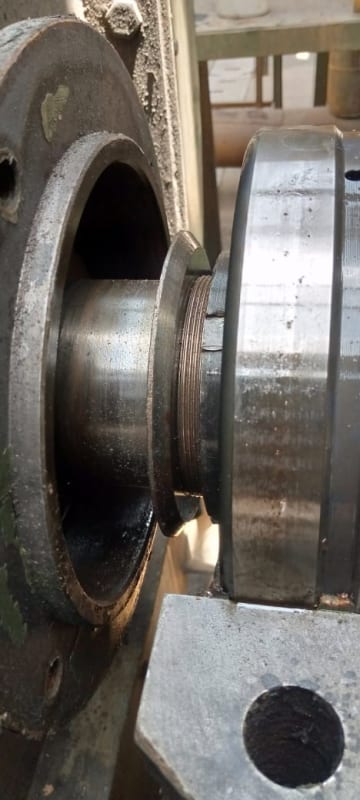